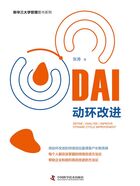
2.3 8D问题解决法
几乎在丰田发展精益理论的同期,受戴明学说的影响,美国福特汽车公司也发展出了一套独特的持续改进体系——8D问题解决法,也称为团队导向问题解决方法,或8D Report,简称8D法,其中的D代表英文单词Discipline(规矩)。福特公司的管理人员希望有一个系统化的方法,可以让设计、制造及生产单位一起处理重复发生的问题。8D法的处理方式是首先找到根本原因,然后采取行动消除根本原因,最后实施永久对策。针对漏失点(也称为逃逸点)的研究可以提升系统侦测错误的能力,即使错误再度发生,也有能力可以检测出来。预防措施也可以找出管理系统中出现上述错误的原因,避免再次发生。
8D法的步骤如下。
·D1成立改善小组。由议题的相关人员组成,通常是跨部门和跨功能性的,明确团队成员之间的分工或担任的责任与角色。小组成员由具有产品或流程专业知识的人员组成。
·D2描述问题。将问题尽可能地量化且清楚地表达,并能解决中长期的问题而不是只解决眼前的问题。可以采用何人(Who)、何事(What)、何地(Where)、何时(When)、为何(Why)、如何(How)及多少钱(How much)——5W2H分析法来识别及定义问题。
·D3实施及确认暂时性的对策。对于D2中的显见问题立即开展快速有效的短期行动,避免问题扩大或持续恶化,其核心是快速行动加快速纠偏。
·D4原因分析及验证原因。发现D2问题的真正原因、说明分析方法、使用工具(品质工具)的应用。所有问题的原因都需要经过确认或证实,不只是单纯的头脑风暴的结果。可以用5Why分析法或是鱼骨图来根据问题或是其影响来标示其原因。
·D5选定及确认长期改善行动效果。拟订改善计划、列出可能的解决方案、选定与执行长期对策、验证改善措施,清除D4发生的真正原因。通常以逐步骤的方式说明长期改善对策,并经过试量产来确认永久对策已经解决客户的问题。
·D6改善问题并确认最终效果。执行D5后进行结果与成效验证。
·D7预防再发生及标准化。制定后续行动方案确保D4的问题不会再次发生,如修改管理系统、操作系统、流程,进行人员教育培训、改善案例分享、作业标准化,分享知识和经验等。
·D8改善小组及规划未来方向。若上述步骤完成后问题已改善,对改善小组的努力进行肯定,并规划未来的改进方向。
在20世纪90年代末,福特公司将8D法升级为Global 8D,使之成为福特公司及其供应链公司的标准,并一直沿用至今。Global 8D主要的优化如下。
增加D0步骤作为流程的开始。在D0步骤中团队需列出此问题的症状,并确认在Global 8D开始前,是否需要采取紧急应变措施。D0步骤也包括了一系统的评估问题,其目的是确认是否需要进行后续的Global 8D流程。
步骤D4~D6增加了标示漏失点程序。漏失点是指整个系统中原本在早期就可能或可以检测出的问题,却没有检测出。此目的不只是考虑根本原因,也考虑系统中是否有未考虑到之处,造成此问题没有检测到。Global 8D在D4步骤就标示及确认漏失点,在步骤D5和D6时,团队需要选择一个永久的改善措施来避免漏失点,并要验证、实行此措施,确认有效。
8D法是基于戴明学说PDCA的深度演进,这种方法简单,是发现根本原因的有效方法,并能够采取针对性措施消除根本原因,执行永久性改善措施。同时,8D法能够帮助探索允许问题逃逸的控制系统。漏失点的研究有助于提高控制系统在问题再次出现时的监测能力。预防机制的研究也有助于帮助系统将问题控制在初级阶段。近年来,8D法在汽车产业以外也开始盛行,随着精益生产及持续改进的应用,8D法也在食品制造、健康护理及高科技产业得到广泛应用。
8D法经常被用来与精益理论做对比。8D法更多地被认为是从解决问题入手的持续改进方法,但不是与企业治理文化、战略管理相匹配的整套理论。8D法强调持续改进的步骤本身,而不是持续改进背后的理念,这使它缺乏戴明学说或精益理论中蕴含的显而易见的管理哲学观。同时,8D法和精益理论一样,缺乏统计管理的一般性原则,在处理大型企业复杂的改进时缺乏效率。