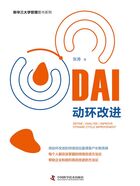
2.2 精益理论
精益理论,也称精益管理,源自精益生产(Lean Production),是衍生自丰田的一种管理哲学。“精益”一词最早出现在麻省理工学院的研究生约翰·克拉富西克于1988年发表的对丰田管理研究的作品中,其中提到“精益生产系统的胜利”。克拉富西克在提出“精益”一词之前,就对丰田的管理哲学做了诸多研究,这些研究进一步引出了美国麻省理工学院的国际汽车计划组织(IMVP, International Motor Vehicle Programme),多位专家和教授历时5年,对全世界17个国家和地区的共计90多个汽车制造厂的调查和对比分析,写出了大量的研究报告,并于1991年出版了名为《改变世界的机器》的著作,定义了一种以丰田管理方式为原型的“精益生产”方式。精益理论由此诞生并开始发展,并且后来在服务业和科技产业领域获得广泛发展与应用。精益理论由最初的在生产系统的管理实践成功延伸到企业的各项管理业务中;也由最初的业务管理具体方法上升为方法论和战略管理理念。
精益理念通过减少经营行为和生产过程中的浪费而实现改进,为客户创造经济价值,使企业的社会性价值实现最大化。因此在精益理论中,消除浪费是改进的第一目标。
在精益理论中,浪费第一次被扩大出3种广义定义,分别是浪费(Muda)、不平衡(Murt)和不均匀(Mura)。同时,浪费的反面是价值增值,精益理论也第一次对“增值”进行了新的定义,即在企业所有的行为或流程中,客户愿意买单的行为或流程。这两个概念的定义,也是后续所有管理理论逐渐形成统一共识的定义,是改进理念的基石之一。这些基本理念,构成了著名的“精益思维”。
精益思维的核心就是消除浪费,提升价值,以最小的资源投入(包括人力、设备、资金、材料、时间和空间),准时(JIT, Just in Time)地创造出尽可能多的价值,并随时随地进行改进,为客户提供新产品和及时的服务。
精益理论中3种浪费的定义如下。
1)浪费(Muda),指在精益管理中,以客户的角度看来,不具有增加价值且可以移除的所有活动,主要有7种,见表2-1。
表2-1 浪费的种类及其描述

2)不平衡(Muri),也称负担,指管理者强加给员工和设备的一些过度的工作要求,主要是由于工作设计缺乏秩序和逻辑而造成的。例如,制造业中的工人过度负重、将生产工具乱搬乱放、危险工作;服务业中超过同伴的工作速度、过度分配资源、业绩指标过高等都会带来这类不平衡的浪费。不平衡是属于超出人体、机器/设备、流程、管理体系承受能力的因素。要消除不平衡,就要整体提高员工的工作效率,而不是针对个体;要求企业不要采取捷径,或者擅自修改决策条件。消除不平衡,最重要的是企业要重视规划和设计。
3)不均匀(Mura),有两个层面的含义:①指各种经营行为之间的不均衡,如销售和生产的不均衡;②指不必要的变化或不一致的管理,主要指在工作设计实施的过程中产生的质量波动和变异,以及管理过程中因不同工具、不同规则、不同编码及不同要求所带来的灾难性后果。
精益理论不仅是汽车制造业的主流管理理论,而且在诸多追求效率、注重质量和成本均衡的公司中得到广泛应用。例如,戴尔、山姆会员店、海尔、格力等公司都是精益理论的践行者和受益者。精益理论提出的“价值”新定义,对信息产业革命中诞生的科技巨头起到了至关重要的指导作用。在“价值增加”理念的指导下,思科、亚马逊、微软等公司迅速形成了自己独有的产品文化和商业逻辑,并在内部策略的改进、组织和流程的设计上,围绕“价值增加”做出了各自的探索。即使这些公司并未对外宣称自己的改进体系是精益理论,但其基础改进理念仍然是基于精益理论的核心理念,这也是精益理论对企业改进的重大贡献。
诸多精益理论的实践者在应用过程中,发现了精益理论在执行中存在的一些风险,主要是杜绝浪费和减少不平衡之间难以实现两全。精益理论要求尽可能地不浪费人力、材料、设备、能源、信息等,实现理想完美的状态,这是精益生产追求的目标和努力的方向。但是在资源方面要求过于苛刻的精简理论本身会导致另一种浪费:即不平衡的出现,这会导致员工的士气下降、忠诚度下降、流失率增加;在材料方面,安全库存和战略储备库存的减少可能给企业造成更大的材料成本损失;在设备方面,一些关键性的设备如果出现备件供应不及时,可能会给企业造成更大的停机损失;在质量控制方面,过激地去掉一些检验环节和人为控制环节,或者成本压缩,将导致企业的质量风险升高;在其他方面同样如此。这种平衡需要高超的管理技巧和实践能力,精益理论的应用不仅需要依赖专家人才的专业知识,而且对实施人员依赖程度很大,一旦人员离职,改进将不能持续。另外,精益理论中的改进工具相对来说比较分散、系统化不强,解决简单问题效率更高,对于复杂问题,效率并不高。由于精益理论缺乏知识的规范性,其实践过程无法保证处于统计受控的状态。