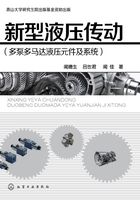
第七节 自冷却理论
本节以斜盘型泵为例,通过建立数学模型并进行推导,定义出两个可以用来衡量轴向柱塞泵自冷却能力的性能指标,并对闭路式泵的典型结构CY14-1型泵和开路式泵的典型结构SPB型泵的自冷却能力分别进行理论分析。
一、传热学理论
(一)传热学基本定理
为了对泵进行自冷却分析和定义,首先应回顾一下热力学的基本方程和定律,才能对以后的研究加以理解。
1.能量守恒定律
能量守恒定律是热力学中最基本的定律,下面分几个方面进行说明。
(1)控制体的能量守恒定律
在应用控制体能量守恒定律时,首先要确定控制体。控制体是由控制面围成的空间区域。因而能量和能量转换均可通过这个控制面进行。就这个控制面而言,在分析斜盘式轴向柱塞泵存油容腔中工作介质的传热问题时,满足能量守恒定律。如果进入控制体的能量超过了流出的能量,则控制体储存(或者说积累)的能量就增加;反之,控制体内储存的能量减少。假若进入的能量等于流出的能量,那么控制体就处于平衡状态,即它所储存的能量是保持总体平衡的(即守恒的)。把能量守恒定律应用于图2-123所示的控制体系,能量守恒的一般形式可以通过速率来表示,其方程为:
(2-252)

图2-123 控制体系能量平衡
式中 ——穿过控制面流入体系的能量速率;
——体系内生成的能量速率;
——流出体系的能量速率;
——体系储存的能量速率。
流入能量速率和流出能量速率
都是表面现象,也就是说,这两项只与在控制表面处发生的过程有关,且流入的能量速率和流出的能量速率均与表面积成正比。在有流体通过控制面时,
和
还包括流体本身带入和带出体系的能量。这些能量一般由动能、势能和热能组成。对于在本节所涉及的问题,通常因为动能和势能与热能相比要小得多,故可以忽略,仅考虑流入和流出控制体积的热能。热能生成项
与其他形式的能量(如化学能、电能、电磁能、核能等)向热能的转换有关,是一种体积现象,即热能在体系内部生成,其生成的速率与体系的体积成正比。本节所考虑的体系,其能量生成项
=0。储存能量的速率
也是一种体积现象,它只与占据控制体的物质的能量增加或减少有关。
(2)表面的能量守恒定律
在以后分析泵壳体外表平均温度时,应用能量守恒定律的情况,控制表面本身不包含体积和质量。因此,能量守恒定律式(2-252)中能量生成项和能量储存项
就变得无意义了,所以只考虑表面现象。此时守恒定律变为:
(2-253)
一般与控制表面有关的传热有三项:介质对控制表面的热传导能量;控制表面对流体的对流传热能量
;控制表面对环境的净辐射传热能量
所组成,它们分别是单位面积上的传热能量。因此,控制表面能量平衡表达式为:
(2-254)
2.傅里叶定律
傅里叶定律能够定量地表述导热过程,计算传热过程的传热量。傅里叶定律可表述为:导热只沿着等温面的法线并朝着温度降低的方向进行。在任何时刻t,均匀连续介质各点就地传递的热流密度,正比于当地的温度梯度,即:
(2-255)
式中 K——傅里叶定律中热导率,W/(m·K)。
式(2-255)中负号表示导热的方向与温度梯度方向相反。
式(2-255)是导热的基本定律,也称傅里叶定律。
3.牛顿冷却定律
对流传热中流体沿固体表面流动时所发生的流体和固体之间热量交换过程中所传递的热量,可以用牛顿冷却定律表达。即对流过程中所传递的热流密度q″与壁面温度Ts和流体温度T∞之差成正比,用公式表示为:
(2-256)
式中 h——传热系数,W/(m2·K)。
如果Ts>T∞,q″>0,说明热量传向流体。
如果Ts<T∞,q″<0,说明壁面吸收热量。
二、热传导方程
1.直角坐标下热传导方程
考虑一种内部存在温度梯度的均匀介质,其温度分布(x,y,z)表示在直角坐标上,如图2-124所示。取一微控制体积dxdydz,由于存在温度梯试,各控制表面都出现传导热交换。传导热流在x、y、z各坐标方向上均与控制面相垂直,并分别用qx、qy、qz表示各坐标方向上的单位热能。因此,在相对的表面上的传导热流可分别表示为:
(2-257)

图2-124 直角坐标上的微元控制体系
介质内部还可能存在与热能生成有关的“能源”项,这一项可表示为:
(2-258)
式中 ——单位容积介质内生成能量的速率,W/m3。
此外,控制体内的物质所储存的热量也在变化,储存的能量项可表示为:
(2-259)
式中 ——单位容积介质的内能随时间的变化率。
对控制体应用能量守恒定律得:
(2-260)
由以上分析可知,热传导速率即构成能量流入项和能量流出项
,因此将式(2-258)和式(2-259)代入式(2-260)有:
(2-261)
将式(2-257)代入式(2-261)得:
(2-262)
利用傅里叶定律式(2-255)求出热传导速度为:
(2-263)
将式(2-263)代入式(2-262)并消去dxdydz有:
(2-264)
式(2-264)就是热传导方程在直角坐标中的一般形式。它是分析热传导问题的一个基本方程。
在一维热传导中(即只在x方向传导),且无能量生成的平衡状态下,式(2-264)可简化为:
这个结果的重要意义在于:在一维稳态、无内生成热的状况下,传导方向上的热流密度是常数,也就是说。
2.柱坐标下的热传导方程
已知某种内部存在温度梯度的均匀介质,其温度分布T(r、φ、z)表示在柱坐标上,如图2-125所示。取一微元控制体drdφdz,由于存在温度梯度,通过诸控制面都出现传导热交换。在r、φ、z各方向传导热流分别与对应控制表面垂直,并分别用qr、qφ、qz表示,因此,在对应表面上的传导热流可分别列为:
(2-265)

图2-125 柱坐标下控制体积简图
介质内部还存在与热能有关的能源项为:
(2-266)
式中 ——单位容积介质的生成能量速率,W/m3。
此外,控制体内物质储存的热量变化为:
(2-267)
式中 ——单位容积介质的内能随时间变化率。
应用控制体积能量守恒定律式(2-252)可知,热传导速率即构成流入能量项和流出能量项
。因此,将式(2-266)和式(2-267)代入式(2-252)得:
(2-268)
将式(2-265)代入式(2-268)得:
(2-269)
利用傅里叶定律式(2-255)求出热传导速率为:
(2-270)
将式(2-270)代入式(2-269),并消去控制体drdφdz,得柱坐标下热传导方程一般形式:
(2-271)
在一维、稳态、无内生成热状况下,式(2-271)可简化为:
(2-272)
式(2-272)表明:在一维、稳态、无内生成热的状况下,传导方向上的热流速率为一常数。
三、一维稳态热传导
一维稳态无内生成热传导系统,介质温度分布及传热速率的求解较简单,且传导模型可以准确地描述许多实际工程系统。譬如,轴向柱塞泵中的斜盘、配流盘、泵壳体的传热过程均可按一维传热系统处理。
(一)一维平壁介质的温度分布及热流速率
在平面壁内进行的一维传导,温度只是x坐标的函数,且传热只在这一个方向进行。如图2-126所示,图2-126(a)为一维平壁传热温度的分布,图2-126(b)所示为一维平壁传热流图。在热流体温度(T∞.1)与平壁一个侧面温度()之间发生对流换热,穿过平壁进行热传导;而在平壁的另一侧(
)和冷却体(T∞.2)之间进行对流换热。

图2-126 平壁传热温度分布及热流速率
1.平壁内的温度分布
对于平壁热传导方程为:
(2-273)
如果壁材料的传热系数K为常数,则对上式进行二次积分,并利用边界条件:T(0)=Tζ.1;T(t)=Tζ.2,求得一维平壁在稳态、无内生成热条件下的温度分布为:
2.平壁传导热流速率qx
利用傅里叶定律式(2-255)求得:
(2-274)
所以
(2-275)
事实上,在求解轴向柱塞泵斜盘、配流盘及泵壳体传热速率时,其内外侧温度qx并非已知,而仅仅已知T∞.1和T∞.2,为此,需要确定qx与T∞.1以及T∞.2之间的数学关系。
3.利用热阻直接求qx
根据傅里叶定律式(2-255)及牛顿冷却定律式(2-256)得:
(2-276)
传导热阻Rcond为:
(2-277)
对流液阻Rconv1及Rconv2有:
(2-278)
(2-279)
总热阻Rtot
(2-280)
因此,一维平壁系统的传热速率可表示为:
(2-281)
(二)径向对称系统温度分布及热流速率
柱形和球形系统常常只在径向存在温度梯度,因此,可以把它们近似看作一维系统。在稳态无内生成热情况下,我们考虑如图2-127所示系统,求解温度分布及热流速率。

图2-127 表面有对流换热的空心圆柱
1.空心圆柱体内温度分布
图2-127(a)是内、外表面分别与温度不同的流体相接触的空心圆柱体。在稳态、无内生成热状况下的热流方程为:
(2-282)
求解式(2-282),并代入边界条件:T(r1)=Tζ.1;T(r2)=Tζ.2,解上述微分方程可得:
(2-283)
2.空心圆柱体的传热速率
根据傅里叶定律式(2-255),传热密度为:
任意半径处热导率qr为:
所以
(2-284)
由式(2-284)可知,一维稳态无生成热径向对称系统的传热率与变量r无关,为一常数。
3.利用热阻求传热速率
一维稳态空心圆柱体,传导热阻为:
(2-285)
对流热阻为:
(2-286)
(2-287)
总热阻为:
(2-288)
因此,空心圆柱体的传热速率可表示为:
(2-289)
四、功率损失分析
本节分析轴向柱塞泵产生功率损失的原因,并推出轴向柱塞泵主要摩擦副功率损失的数学表达式,运用能量观点,求解各摩擦副功率损失后的油液平均温度。
(一)产生功率损失的原因
轴向柱塞泵的功率损失主要包括以下几方面:
ΔWg——由于轴向柱塞泵各摩擦副配合间隙有压力油液的泄漏而产生的功率损失;
ΔWu——由于液压油黏性摩擦产生于具有相对运动表面的黏性摩擦功率损失;
ΔWe——由于工作油液的压缩与膨胀而产生的功率损失;
ΔWp——与压力有关的摩擦功率损失,如发生在轴承处的摩擦功率损失,作用在柱塞上的侧向力,使柱塞与缸体孔单侧接触产生的摩擦功率损失等;
ΔWc——其他功率损失,如球铰摩擦损失和油液从入口流到出口的流体阻力所造成的功率损失等,这些功率损失一般相对于其他功率损失来讲比较小,有时可忽略不计。
因此,轴向柱塞泵总功率损失ΔW可表示为:
(2-290)
由于本节主要研究对象是斜盘型轴向柱塞泵存油容腔油液温度的时变规律,因此只讨论与油液温度有关的主要摩擦副的功率损失情况。
(二)主要摩擦副功率损失分析
1.斜盘、滑靴间功率损失分析及温升
由于闭路式轴向柱塞泵与开路式轴向柱塞泵的主要差别是滑靴与斜盘这对摩擦副。为了说明问题方便起见,这里以闭路式的典型结构之一CY14-1轴向柱塞泵和开路式的典型结构之一SPB轴向柱塞泵为例进行分析。
(1)CY型泵斜盘、滑靴间功率损失分析
①泄漏损失ΔWg。图2-128所示为CY泵简化型滑靴结构。由《液压流体力学》可知,两平行平板间的放射流动流量公式为:
(2-291)

图2-128 CY型简化后的滑靴柱塞组
式中 δ——平行圆盘间间隙,mm;
Δp——压差,Pa;
R1,R2——内、外密封带半径,m;
μ0——油液动力黏度系数。
将式(2-291)应用于图2-128所示的斜盘、滑靴间可得到CY泵斜盘与滑靴间单个滑靴泄漏量。
(2-292)
式中 ΔQ'——斜盘与滑靴间泄漏量,L;
pr——滑靴油室内压力,Pa;
p0——泵壳体内存油腔内油液压力,Pa。
设处于压油区的滑靴为个,则CY泵斜盘、滑靴处总漏流量ΔQ1为:
(2-293)
式(2-293)对于偶数泵取则为:
因此,可写出CY泵斜盘、滑靴间总泄漏功率损失,对于奇数柱塞泵为:
(2-294)
对偶数柱塞泵为
(2-295)
②斜盘与滑靴间黏性摩擦功率损失。滑靴在斜盘表面绕o点做椭圆运动,图2-129所示为滑靴功率损失计算图。

图2-129 滑靴摩擦功率损失计算
滑靴沿斜盘滑行时的黏性摩擦功率可由下式决定:
(2-296)
式中 vs——滑靴沿斜盘表面的滑行速度,m/s。
所以式(2-296)变为:
(2-297)
式中 ω——滑靴绕o点的滑行角速度;
——单个滑靴、斜盘黏性摩擦功率损失;
ρ——滑靴运行轨迹的向径,m;
δ1——滑靴平面与斜盘表面间间隙,mm。
因此,处于压油区的CY泵斜盘与滑靴处总的黏性功率损失:
当高压区有个柱塞时:
(2-298)
当高压区有个柱塞时:
(2-299)
又因为
所以奇数时,式(2-299)变为:
(2-300)
偶数时:
(2-301)
所以CY泵斜盘与滑靴处总的功率损失,在柱塞数为奇数时为:
(2-302)
柱塞数为偶数时:
(2-303)
③经斜盘、滑靴间泄漏损失后的油液温度。滑靴、斜盘这对摩擦副所产生的功率损失为ΔW1,实际上基本转变成热能而使间隙中油液内能增加,表现为油液湿度上升。高温热油在液压力作用下,泄漏到泵壳体存油容腔,仅有极少部分热能通过边界壁面散失到周转油液中去或转变为噪声、振动等。一般情况下,这部分热能与油液湿度升高的热能相比,可以忽略不计。即认为斜盘、滑靴间产生的功率损失ΔW1全部转变成热能,使泄漏油液的温度升高。设油液初始湿度为T0(℃),温度升高后变为T1(℃)。并认为油液具有常物性,即ρ、cp为常量,则根据能量守恒定律有:
(2-304)
解得
(2-305)
将式(2-302)、式(2-303)代入式(2-305),当柱塞数为奇数时有:
(2-306)
当柱塞数为偶数时有:
(2-307)
式中 ρ——油液密度;
cp——油液定压比热容。
(2)SPB泵斜盘、滑靴间功率损失分析
对于SPB泵来说,简化后的滑靴和斜盘副如图2-130所示。对于同一流量规格的SPB泵和CY泵相比,滑靴与柱塞的主要区别是将CY泵中柱塞和滑靴的阻尼孔变为通孔,由于直径增大得很多,故滑靴油腔内的压力比CY泵大得多,不是pr,而是输出压力ps。

图2-130 简化型SPB泵滑靴功率损失计算图
①对于SPB泵斜盘、滑靴间的泄漏损失,同样根据《液压流体力学》两平行平板间圆盘的放射流量方程,可得SPB泵单个滑靴与斜盘间泄漏流量为:
(2-308)
同理SPB泵斜盘与滑靴副间总的泄漏量和总的泄漏损失有柱塞数为奇数时分别为
(2-309)
(2-310)
当柱塞泵柱数为偶数时:
(2-311)
(2-312)
②对于SPB泵斜盘、滑靴间黏性摩擦功率损失,在相同工况下,可以认为SPB泵斜盘、滑靴间黏性摩擦功率损失与CY泵相同,即奇数柱塞时有:
(2-313)
偶数柱塞时有
(2-314)
所以SPB泵斜盘与滑靴副总的功率损失在奇数柱塞时为:
(2-315)
偶数时为:
(2-316)
③经SPB泵斜盘、滑靴间泄漏损失后的油液温度。
同理,运用能量观点,忽略其他能量损失,则认为SPB泵斜盘与滑靴间功率损失全部转变成热能,使间隙中油液温度升高,根据能量守恒定律有:
(2-317)
求解式(2-317)得:
(2-318)
将式(2-315)、式(2-316)代入式(2-318),在柱塞数为奇数时:
(2-319)
柱塞数为偶数时:
(2-320)
式中 T1s——经SPB泵斜盘与滑靴间泄漏损失后的油液温度;
——SPB泵斜盘、滑靴间泄漏流量,L。
2.柱塞、缸体间的功率损失及温升
由于CY泵和SPB泵在这个间隔的情况基本相同,故不必分别考虑,只要统一考虑即可。
(1)柱塞、缸体间的泄漏损失
设轴向柱塞泵缸体腔室内压力为ps,柱塞在缸体内是平行无偏斜放置的,半径方向的间隙为δ2时,柱塞与缸体间单柱塞的泄漏量为:
(2-321)
式中 δ2——柱塞与缸体孔间的径向间隙,m;
l——柱塞与缸体孔的含接长度,m;
d——柱塞直径,m;
——单柱塞在缸体与柱塞的泄漏量,L。
那么,处于压油区所有的柱塞与缸体之间的总的泄漏量和总的功率损失,在奇数时分别为:
(2-322)
(2-323)
偶数柱塞时分别为:
(2-324)
(2-325)
(2)柱塞、缸体间的黏性摩擦功率损失
轴向柱塞泵中柱塞与缸体副黏性摩擦情况计算简图,如图2-131所示,根据流体力学理论可写成下式:
(2-326)

图2-131 柱塞、缸体副黏性摩擦功率损失计算简图
式中 vp——柱塞相对于缸体的运动速度,m/s。
处于压油区的柱塞因黏性摩擦力ΔF2所损耗的平均摩擦功率为:
(2-327)
因为
代入式(2-327)积分得:
(2-328)
当柱塞数为奇数时,将z=z+1代入即可。又因为理论排量所以有:
(2-329)
式中 lH——斜盘倾角α=0时,柱塞与缸体的含接长度。
所以,轴向柱塞泵中缸体、柱塞间总的功率损失为:
(2-330)
当柱塞为奇数时有:
(2-331)
当柱塞数为偶数时:
(2-332)
(3)柱塞、缸孔间泄漏损失的油液温升
如果忽略由于接触壁面的传热影响,即认为柱塞与缸体副的功率损失全部使间隙中油液的内能增加,表现为油液温度上升,并以热油形式泄漏到泵壳体的存油容腔中。设间隙油液初始温度为T0(℃),变化后的油液温度为T2(℃),并设油液密度为ρ,定压比热容为cp,且ρ,cp为常数,则有:
(2-333)
解式(2-333):
(2-334)
将式(2-331)、式(2-332)代入式(2-334),若为奇数柱塞时有:
(2-335)
偶数柱塞时有:
(2-336)
3.配流盘、缸体间功率损失及温升
(1)配流盘、缸体间的泄漏功率损失
图2-132所示为配流盘的结构尺寸图,它与缸体之间的泄漏量可近似如下计算:
(2-337)

图2-132 配流盘结构尺寸图
式中 δ3——缸体与配流盘间的间隙;
R1,R2,R3,R4——配流盘内、外封油带尺寸;
φ0——配流盘封油角度,rad;
ps——泵输出压力,Pa;
p0——泵壳内压力,Pa。
因此,摩擦副的泄漏功率损失为:
(2-338)
(2)配流盘、缸体间黏性摩擦功率损失
在配流盘与缸体之间间隙内的油膜中,取一厚度为Δ的微元体(Δ为配流盘与缸体之间距离),配流盘与缸体之间的黏性摩擦转矩为:
因为
所以
(2-339)
式(2-339)以整个接触面为积分区域进行积分得:
(2-340)
如果配流盘、缸体间的间隙为δ3,则配流盘,缸体的黏性摩擦功率损失为:
(2-341)
以上讨论的式(2-340),也存在奇数和偶数柱塞问题,这里不再详述。
(3)配流盘、缸体间泄漏损失的油液温升
同理,忽略由于接触壁面的传热影响,认为配流盘、缸体间能量损失全部转换成热能,使间隙内油液内能增加,表现为油液温度上升,以热油形式泄漏到泵壳体内的存油容腔。设油液初始温度为T0(℃),温升后变为T3(℃),且液体密度ρ,定压比热容cp为常量时有ρcpΔQ3(T3-T0)=ΔW3。
所以:
(2-342)
将式(2-338)和式(2-340)代入式(2-342)有:

4.缸体、泵壳间油液黏性摩擦功率损失
如果缸体与壳体间油液的黏性摩擦功率损失是由于缸体与壳体间间隙小,而且缸体又高速旋转,那么其间的黏性摩擦转矩便不可忽略,其值由《液压流体力学》可得:
(2-343)
式中 δ4——缸体与泵壳之间的半径方向间隙,m;
D2——缸体外径,m;
l0——缸体长度,m。
因此,缸体与泵壳之间的黏性摩擦功率损失为
(2-344)
五、CY型泵自冷却分析
本节采用在泵体简化图上分块划分控制体积的方法,利用控制体积能量守恒定律,求解各控制体积油液温度的瞬时变化规律,定量分析CY型轴向柱塞泵的自冷却性能。
(一)CY泵存油容腔控制体积的划分
所谓CY泵存油容腔,指的是滑靴、斜盘、缸体、配流盘等与泵壳体组成的容腔。分析研究这部分油液的温升规律,对改善CY泵自冷却状况,提高使用寿命,具有重要实际意义。
首先把CY泵如图2-133那样简化,并将泵的存油容腔划分成三块控制体积,对每块控制体积采用温度均值来表征控制体积的油液温度,求解各控制体积的油液温度变化规律。在求解时基于如下假设:

图2-133 CY泵存油容腔控制体积的划分
ΔW1,ΔW2—摩擦副功率损失;ΔQ1—摩擦副泄漏流量;Vc1—划分的控制体积;ΔQc1—控制体积;T1—摩擦副泄漏油液温度;Tc1—控制体积Vc1处的油液温度
工作介质即油液具有常物性,也就是说油液密度ρ、黏度μ0、压力p、定压比热容cp为常量,不随时间、空间、温度变化而变化。
控制体积内油液热变换均匀,其温度仅是时间的函数,即Tc=Tc(t)。
用温度平均值来描述控制体积油液温度,忽略其内部实际上存在的温度梯度。
至于每块控制体积的特点及能量框图,将在下面给予详细论述。
(二)各控制体积油温的时变规律
1.控制体积Vc1油温的时变规律
(1)控制体积Vc1的特点
控制体积Vc1具有如下特点:
①控制体积Vc1内,有内生成热元件,即斜盘、滑靴间和柱塞、缸体间产生的热能大体以高温热油的形式进入控制体积Vc1中,极少部分热能通过摩擦副传导散失到Vc1中。
②流出控制体积Vc1的流量ΔQc1进入控制体积Vc0中。
(2)控制体积Vc1的能量框图
流入控制体积Vc1的能量项为:
流出控制体积Vc1的能量项为:
控制体积Vc1能量生成项为:
控制体积Vc1能量储存项为:
根据能量守恒有:
(2-345)
式中 qs1——流入控制体积Vc1内的斜盘、滑靴间泄漏损失油液所具有的能量速率;
qc1——流入控制体积Vc1内的缸体、柱塞间泄漏损失油液所具有的能量速率;
qscond——流入控制体积Vc1内的斜盘、滑靴间热传导能量速度率;
qp10——与控制体积Vc1接触的泵壳Ⅰ段,由对流散热而流出Vc1的能量速率;
qc10——流出控制体积Vc1的油液本身具有的能量速率;
Hc1——流出控制体积Vc1的其他能量损失;
qc1st——控制体积Vc1内储存内能的速率。
如将式(2-345)用能量框图表示的话,可简化成如图2-134所示的控制体积Vc1的能量框图。

图2-134 控制体积Vc1的能量框图
(3)求各能量速率项的具体表达式
①求qs1、qc1、qc10。在式(2-345)中qs1、qc1表示流入控制体的能量项,qc10表示流出控制体积Vc1的能量项,这几项可以分别如下表示:
(2-346)
(2-347)
(2-348)
式中 T1——斜盘、滑靴间泄漏油液温度, ℃;
T2——缸体、斜盘间泄漏油液温度, ℃;
Tc1——Vc1体积内油液任意时刻t的温度, ℃;
Q1——斜盘、滑靴间泄漏油液流量,L;
Q2——缸体、斜盘间泄漏油液流量,L;
Qc1——控制体积Vc1流出的油液流量,L。
根据流量连续性方程有:
(2-349)
②求qscond。图2-135(a)为斜盘简化传热图,图2-135(b)为按简化后的斜盘画出的传热流图,可直接写出斜盘的传热速率:
(2-350)

图2-135 斜盘及其传热简图
式中 h0——油液的对流换热系数;
K——斜盘传热系数。
其余符号同前。
为了说明斜盘内、外侧温度Ts1s1、Ts1s2和Tc1及T1 的密切关系,现推导如下,由式(2-276)可知:
(2-351)
令ls1h0/K=βs,并简化式(2-351),则有:
(2-352)
(2-353)
若用矩阵表示则为:
(2-354)
由式(2-354)可以清楚地表明Ts1s1、Ts1s2与Ts1、T1的密切关系。为了提高斜盘的使用寿命,应尽可能降低Ts1s1、Ts1s2,以减少热变形对寿命的影响。对CY泵来讲,应尽可能降低Tc1以及尽量减少摩擦功率损失。
同理可计算出由于滑靴的热传导而进入控制体积Vc1的能量速率qsconv2为:
(2-355)
式中 ls2——滑靴厚度;
As2——滑靴传热面积,m2。
滑靴可简化成如图2-136(a)所示的平板,其传热流图如图2-136(b)所示。因此斜盘、滑靴间总传热速率为:
(2-356)

图2-136 滑靴传热简图
式中
③求qp10。图2-137所示为泵壳Ⅰ段传热流图,利用式(2-289)可直接写出对流换热速率qp10为:
(2-357)

图2-137 泵壳Ⅰ段传热流图
式中 r1——泵Ⅰ段内侧半径,m;
T∞——环境温度, ℃;
r2——泵壳Ⅰ段外半径,m;
Kp——泵壳材料传热系数;
ha——空气换热系数;
h0——油液换热系数;
l1——与控制体积相接泵壳Ⅰ段长度,m。
因为:
(2-358)
所以可求出Tp1s1、Tp1s2与Tc1、T∞的数学关系式为:
(2-359)
(2-360)
用矩阵表示为
(2-361)
式中 Rconv11——控制体积Vc1油液对泵壳Ⅰ段对流液阻;
Rconv12——空气对泵壳Ⅰ段对流液阻;
Rcond1——泵壳传导液阻;
Rptot1——泵壳Ⅰ段总热阻。
④求qc1st。设控制体积Vc1的容积为V1,油液密度为ρ,定压比热容为cp,任意时刻t时,控制体积的油温为Tc1,则有:
(2-362)
(4)建立控制体积Vc1油温时变模型并求解
将式(2-346)~式(2-348)、式(2-350)、式(2-357)、式(2-362)代入式(2-345)得:
(2-363)
整理得标准形式微分方程,即:
(2-364)
并令:
(2-365)
(2-366)
则式(2-364)可简化为:
(2-367)
求解上述微分方程得:
(2-368)
利用初始条件Tc(0)=T0代入式(2-368)有:
所以式(2-367)的解为:
(2-369)
这就是CY泵控制体积Vc1存油容腔油液温度的瞬态变化规律。
利用式(2-361)和式(2-354),可分别求得CY泵的斜盘与泵壳Ⅰ段内、外表面平均温度的瞬态变化规律。
(2-370)
(2-371)
(5)结果分析
最高温升,表征了控制体积Vc1油温上升的程度,
表征了控制体积Tc1油温变化的快慢程度。为了便于分析比较CY泵各控制体积的油液温升幅度及温升速率,故定义如下。
最高温升幅度为:
(2-372)
温升速率为:
(2-373)
下面分别求出控制体积、油液最高温升幅度,以及温升速率KTc1。
最高温升幅度为:
(2-374)
事实上,由于泵壳体以及斜盘与滑靴副传热影响相对于泄损发热较小,故式(2-374)可简化为
(2-375)
将式(2-375)变形,并利用式(2-304)、式(2-333)可得:
(2-376)
式(2-376)表明控制体积Vc1油液最高温升幅值与流出Vc1油液的流量ΔQc1成正比,因此,提高控制体积Vc1的本身自冷却流量ΔQc1,可以降低Vc1油液温升的幅值。
控制体积Vc1油液温升速率KTc1为:
(2-377)
如果采用求ΔTmc1时的方法,则式(2-377)变为:
(2-378)
从式(2-378)也可以看出提高控制体积Vc1的自冷却流量ΔQc1,可以降低油液温升速率。

图2-138 Tc1随时间变化的曲线
2.控制体积Vc2油液温度变化规律
(1)控制体积Vc2的特点
①控制体积Vc2内有生成热元件,即缸、配流盘摩擦副。它们所产生的热能大都以高温热油的形式进入控制体积Vc2内,另有很少部分则通过摩擦副传导散入到Vc2内。
②流出控制体积Vc2的流量ΔQc2进入控制体积Vc0。
(2)控制体积Vc2能量框图
流入控制体积Vc2的能量项为:
流出控制体积Vc2的能量项为:
控制体积能量生成项为:
控制体积Vc2的能量储存项为:
根据能量守恒定律:
则有:
(2-379)
式中 qoi——流入控制体积Vc2的缸体、配流盘间泄漏油液所具有能量速率;
qoc——由于Vc2油液与配流盘副对流散热,而进入Vc2的传热速率;
qc20——流出Vc2的油液本身所具有的能量速率;
qp20——与控制体积Vc2接触的泵壳Ⅱ段,由于Vc2油液对流换热而流出的传热速率;
Hc2——其他因素产生于Vc2内的能量损失(略);
qc2st——控制体积Vc2内能的增加速率。
如果用能量框图表示,则可用如图2-139所示的简化后的Vc2能量框图。

图2-139 控制体积Vc2的能量框图
(3)求各能量项具体表达式
①求qoi、qc20。设缸体、配流盘间泄漏损失的液体温度为T3,泄漏流量为ΔQ3,控制体积Vc2的自冷却流量为ΔQc2,那么有:
(2-380)
②求qoc。配流盘传热流图如图2-136(b)所示。由式(2-380)可直接求出qoc。
(2-381)
式中 Rotot——配流盘总液阻。
(2-382)
式中 A0——配流盘传热面积;
l0——配流盘厚度;
K0——配流盘材料传热系数。
由傅里叶定律及牛顿冷却定律得:
(2-383)
简化上式,并设:
则有:
(2-384)
(2-385)
写成矩阵表达式有:
(2-386)
③求qp2。图2-140所示为与控制体积Vc2接触的泵壳Ⅱ段的传热流图。利用式(2-380)可直接求出对流换热速率为:
(2-387)

图2-140 配油盘传热流图
式中 l2——与控制体积Vc2接触的泵壳Ⅱ段长度,m。
由傅里叶定律及牛顿定律得:
(2-388)
式中 Tp2s1——泵壳体Ⅱ段内表面温度, ℃;
Tp2s2——泵壳体Ⅱ段外表面温度, ℃;
Rconv21——控制体积Vc2对泵壳Ⅱ段对流液阻;
Rconv22——空气对泵壳Ⅱ段的对流热阻;
Rcond2——泵壳Ⅱ段传导热阻。
设Rptot为泵壳Ⅱ段总热阻,则:
由式(2-388)求得Tp2s1、Tp2s2与Tc2、T∞之间的数学表达式:
(2-389)
(2-390)
写成阵矩表达式有:
(2-391)
④求qc2st。如图2-141所示,设控制体积Vc2的容积为V2,温度为Tc2,则任意时刻t时有:
(2-392)

图2-141 泵壳Ⅱ段的传热流图
(4)建立Vc2油液温度微分方程并求解。
将式(2-380)、式(2-381)、式(2-388)、式(2-392)代入式(2-379)有:
(2-393)
整理成标准形式:
(2-394)
令
(2-395)
(2-396)
因此方程式(2-394)可改写为:
(2-397)
解上述方程并代入初始条件得:
(2-398)
式中 T0——Vc2油液t=0时油温,Tc2(0)=T0。
将式(2-398)代入式(2-386)和式(2-391)即得到配流盘与泵壳体Ⅱ段内、外表面平均温度随时间变化规律。
(2-399)
(2-400)
(5)结果分析
如图2-142所示,作出式(2-398)在直角坐标系下的图像。由图2-142可知,控制体积Vc2的变化规律与Vc1有完全相同的形式,其规律由以上证明可求得最高温升幅度及温升速率。

图2-142 控制体积Vc2油液温度变化曲线
①Vc2最高温升幅度ΔTmc2
(2-401)
忽略泵壳体及配流盘传热影响,则式(2-401)可以简化为:
(2-402)
利用流量连续性方程ΔQc2=ΔQ3,式(2-402)为:
(2-403)
式(2-403)表明:控制体积Vc2最高温升幅度与流出Vc2油液流量即Vc2的自冷却油液流量成正比。如增大ΔQc2,则可有效地降低Vc2油液温升幅度。
②求Vc2温升速率
对式(2-398)求导,即得KTc2:
(2-404)
如果忽略泵壳体与斜盘对流散热影响,则式(2-404)变为:
(2-405)
式(2-405)表明增大控制体积Vc2的自冷却流量ΔQc2也可以减缓Vc2油液温度上升速率。
3.建立Vc0油液温升微分方程及求解
(1)控制体积Vc0的特点
①控制体积Vc0内有生成热,即由于控制体积Vc0内油液黏性摩擦功率损失ΔW4产生热能使Vc0内的油液温度上升。
②流出控制体积Vc0的油液流量ΔQc0经泄漏回油管路回油箱。
(2)控制体积Vc0的能量框图流入控制体积Vc0的能量项为:
流出控制体积Vc0的能量项为:
控制体积Vc0的能量生成项为:
控制体积Vc0的能量储存项为:
根据控制体积能量守恒定律:
有如下方程:
(2-406)
式中 qc10——由控制体积Vc1流入控制体积Vc0的油液(ΔQc1,Tc1)所具有的能量速率;
qc20——由控制体积Vc2流入控制体积Vc0的油液(ΔQc2,Tc2)所具有能量速率;
qp30——控制体积Vci对应的泵壳Ⅲ段对流散热速率;
qcyr——控制体积Vc0内的油液,因缸体高速旋转及油液的黏性摩擦剪切而产生热能的能量速率;
qcyc——缸体与柱塞副产生的热能经缸体传到控制体积Vc0的能量速率;
qc00——流出控制体积Vc0液体所具有的能量效率;
Hc0——由于其他原因而损失的能量(略);
qcost——控制体积Vc0内能量储存速率。
将式(2-406)用能量框图表示,如图2-143所示。

图2-143 控制体积Vc0的能量框图
(3)求各能量项的具体表达式
①求qc10、qc20、qc00。如图2-144所示,设在任意时刻t内,从Vc1流入Vc0的油液液体温度为Tc1,流量为ΔQc1;从Vc2流入Vc0的油液温度为Tc2,流量为ΔQc2。那么就有:
(2-407)
(2-408)
(2-409)

图2-144 泵壳Ⅲ段的传热流图
②求qcyr。如前所述其能量速率
(2-410)
③求qcyr、Hc0。一般情况下,这两项相对于其他能量项很小,故这里忽略不计。
④求qp30。可以直接画出泵壳Ⅲ段的传热流图和对流散热速率为:
式中 Rptot3——与控制体积Vc0相接触的泵壳Ⅲ段总热阻。
(2-411)
式中 Rconv31——Vc0油液与泵壳Ⅲ段对流换热热阻;
Rconv32——空气对泵壳Ⅲ段对流换热热阻;
Rcond3——泵壳Ⅲ段导热热阻。
(2-412)
(2-413)
(2-414)
根据傅里叶定律及牛顿冷却定律得:
(2-415)
式(2-415)变形可求得:
(2-416)
(2-417)
其矩阵形式有:
⑤求qcost。设控制体积Vc0的容积为V0,时刻t时控制体积Vc0的油液温度为Tc0,则有
(2-418)
(4)建立Vc0油液温度微分方程及求解
将式(2-409)~式(2-411)、式(2-418)代入式(2-406)得:
(2-419)
整理得
(2-420)
令
(2-421)
(2-422)
由式(2-422)可知,q0并非常数,而是时间的函数,即q0=q0(t)。有:
(2-423)
令
(2-424)
(2-425)
因此式(2-420)变为:
(2-426)
可得泵壳体Ⅲ段内、外表面平均温度值Tp3s1、Tp3s2,并可写成矩阵表达式。
(2-427)
(5)结果分析
在直角坐标系内作出式(2-426)的图像,如图2-145所示。由图中可以看出,由于控制体积Vc1和Vc2对控制体积Vc0的影响,即有热能通过油液流入控制体,使得泵存油容积的总能量变化,以Vc0内油液温度上升的形式表现在Vc0控制体积内,关于这一点,可以从Vc0的油液最高温度值来验证。

图2-145 控制体积Vc0的油温变化曲线
①Vc0最高温升幅度ΔTmc0。
(2-428)
将式(2-421),式(2-424)代入式(2-428)并忽略传热等因素的影响,可得:
(2-429)
(2-430)
由式(2-430)可知,提高Vc0的自冷却流量ΔQc0,可以降低Vc0内油液的温升幅度。
②求温升速率KTc0根据温升速率的定义,由:
求得:
(2-431)
利用式(2-431)可求任意时刻Vc0内油液温升速率。
(三)结论
通过对CY泵控制体积内工作介质油液温度的时变规律分析,求出了存油容腔中油液温升的瞬时变化规律及其自冷却性能的衡量指标,现分别总结如下。
①CY型轴向柱塞泵的三对摩擦副,即斜盘与滑靴副、柱塞与缸体副、缸体与配流盘副的功率损失,以及缸体与泵壳之间间隙所组成的存油容腔中油液的黏性摩擦功率损失是轴向柱塞泵存油容腔中油温升高的主要原因。
②由于存于油腔中的液压油温度上升,CY泵中三对主要摩擦副由于表面温差的不同,将产生不同程度的热变形。随着摩擦副的高速旋转,加剧了其各摩擦面的磨损,严重影响了轴向柱塞泵的使用寿命。
③CY型轴向柱塞泵内存油容腔中各控制体积油液的温度随时间呈负指数曲线单调增加,且存在一个极限温度值ΔTm。
④提高各控制体积的自冷却流量,不但可以降低最高温升的幅度,而且还可以减缓油温升高的速率。
⑤我们可以将最高温升幅度ΔTm和温度上升速率KT作为两个衡量轴向柱塞泵自冷却能力的标准,用于轴向柱塞泵自冷却的设计和同类产品自冷却能力的比较。
⑥CY型轴向柱塞泵的自冷却性能是相当低的,这是因为CY泵的自冷却流量与泵的容积效率ηV是密切相关的,设CY泵理论流量为QT,容积效率为ηV,自冷却流量为ΔQ,则有:
由前分析可知,提高CY泵各控制体积的自冷却流量ΔQci,可以降低最高温升幅度ΔTm及温升速率KT,但是ΔQci增加,则使ηV大大降低,这是不允许的。因此,使得靠增加CY泵的泄漏流量ΔQ使泵自冷却是相当有限的,必须采用其他措施解决这个矛盾。
六、SPB型泵自冷却分析
本节在上节分析CY型轴向柱塞泵自冷却能力的基础上,建立SPB型开路式泵存油容腔工作介质温度的微分方程,并求解得出温度的时变规律,进而分析SPB泵的自冷却性能。
(一)SPB泵控制体积的划分
从前述分析可知,SPB泵与CY泵相比,它们的主体结构相同,配流原理不同。SPB泵采用双端面配流,双通道供油,靠吸油实现自冷却,因此,SPB泵存油容腔油液控制体积的划分与CY泵相同,如图2-146所示为简化后的SPB泵控制体积的划分情况。

图2-146 SPB泵控制体积的划分
Ts1—SPB泵段控制体积油液温度;ΔQs1—SPB泵段控制体积自冷却流量;ΔQc—由泵吸油分流到存油容腔中的冷却流量
在后面章节中建立控制体积油液温度微分方程时,均采用与CY泵相同的分析方法,即能量守恒定律及集总热容法。因此,在SPB泵自冷却能力分析过程中,仅将SPB泵与CY泵不同之处予以论述,余者直接写出结果,进行分析论证。
(二)SPB泵各控制体积变化规律
1.控制体积Vc2的油液变化规律
(1)控制体积Vc2的特点
①控制体积Vc2内有生成热元件,即缸体与配流盘之间这一对摩擦副。
②来自泵体吸油口分流流量ΔQc(即自冷却流量)流入控制体积Vc2,流出Vc2油液流量ΔQc2进入控制体积Vc0。
(2)控制体积Vc2的能量框图
流入控制体积Vc2的能量项:
(2-432)
流出控制体积Vc2的能量项:
(2-433)
控制体积Vc2的能量生成项:
控制体积Vc2的能量储存项:
(2-434)
根据能量守恒定律:
则有:
(2-435)
将式(2-435)用能量框图表示,如图2-147所示。从图中可知,流入控制体积Vc2的能量项比CY泵多了一项qci,该项可表示为:
(2-436)

图2-147 SPB泵控制体积Vc2的能量框图
将相应公式代入式(2-435),并忽略Hc2项有:
(2-437)
令
(2-438)
(2-439)
将式(2-438)、式(2-439)代入式(2-437)有:
(2-440)
解式(2-440)得:
(2-441)
于是便得到了SPB泵、泵壳体Ⅱ段内、外表面平均温度随时间变化规律,同样可用矩阵表示:
(2-442)
(2-443)
(3)结果分析
在直角坐标系下作出图形如图2-148所示。根据前述的定义可以求出最高温升幅度ΔTms2及温升速率KTs2。

图2-148 直角坐标系下SPB泵油温变化曲线
①最高温升幅度ΔTms2
(2-444)
忽略由于油液与配流盘、泵壳体对流换热等影响后有:
(2-445)
对控制体积应用流量连续性原理有:
(2-446)
将式(2-446)代入式(2-445),又因为:
得到:
(2-447)
式中 ΔQs2——Vc2的自冷却流量。
从式(2-447)可知,SPB泵最高温升幅度表达式与CY泵具有完全相同的形式,不过SPB泵自冷却流量ΔQc2≫ΔQs2,又因为:
所以有:
也就是说,在控制体积Vc2中的液体温度SPB泵远低于CY泵。
②温升速率。对式(2-441)求导,并忽略对流换热影响有:
(2-448)
式(2-448)表明,提高ΔQs2可以卓有成效地减缓控制体积Vc2油液温升速率。
2.控制体积Vc0油夜时变规律
(1)控制体积Vc0的特点
①控制体积Vc0有生成热,即由于控制体积Vc0的油液黏性剪切作用及缸体的高速旋转产生的热能作用于Vc0,使Vc0内油温上升。
②流出控制体积Vc0的流量ΔQc进入控制体积Vc1。
(2)控制体积Vc0的能量框图
流入控制体积Vc0的能量项:
(2-449)
流出控制体积Vc0的能量项:
(2-450)
控制体积Vc0能量生成项:
(2-451)
控制体积Vc0能量储存项:
(2-452)
根据能量守恒定律:
有:
(2-453)
式中
(2-454)
(2-455)
(2-456)
(2-457)
(2-458)
(2-459)
(2-460)
将式(2-453)用能量框图表示如图2-149所示。

图2-149 控制体积Vc0能量框图
(3)建立Vc0的油温微分方程并求解
将相应公式代入(2-453)可得:
(2-461)
令
(2-462)
(2-463)
由式(2-463)可知,qs0不是常数,而是时间的函数,即:
得
(2-464)
令
(2-465)
(2-466)
将式(2-464)~式(2-466)代入式(2-462)有:
(2-467)
因此,Vc0油液温度微分方程变为:
(2-468)
解上式有
(2-469)
利用初始条件Ts0(t)|t=0=T0,确定常数C1:
(2-470)
所以:
(2-471)
将式(2-471)代入式(2-470)得:
(2-472)
这就是SPB泵控制体积Vc0油液温度瞬态变化规律。同样可以求得泵壳体Ⅲ段内、外表面平均温度随时间变化规律。用矩阵表示有:
(2-473)
(4)结果分析
在直角坐标上作出式(2-472)的图形,如图2-150所示。由以前的定义同样可以求出最高温升幅度及温升速率。

图2-150 控制体积Vc0油温变化曲线
①最高温升幅度ΔTmso。
忽略泵壳传热影响,则ΔTmso为:
(2-474)
对控制体积应用连续性方程有:
(2-475)
(2-476)
②温升速率KTso
对式(2-472)求导得:
(2-477)
3.控制体积Vc1的油温微分方程及求解
(1)控制体积Vc1的特点
①控制体积Vc1内有生成热元件,即斜盘、滑靴间及柱塞缸体间这两对摩擦副,产生的功率损失都转化为热能,以油液温度上升的形式流入控制体积Vc1。
②自冷却流量来自于控制体积Vc0,流出控制体积Vc1的油液经倾斜配流盘上吸油窗口,进入轴向柱塞泵的柱塞腔内。
(2)控制体积Vc1的能量框图
流入控制体积Vc1的能量项:
(2-478)
流出控制体积Vc1的能量项:
(2-479)
控制体积Vc1的能量生成项:
控制体积Vc1的内能量储存项:
(2-480)
根据能量守恒定律:
有:
(2-481)
(2-482)
(2-483)
(2-484)
(2-485)
(2-486)
(2-487)
(2-488)
(2-489)
用能量框图表示,如图2-151所示。

图2-151 控制体积Vc1能量框图
(3)建立Vc1的油液微分方程并求解
(2-490)
令:
(2-491)
(2-492)
由式(2-492)可见,qs1不是常数,即:
有:
(2-493)
令
(2-494)
(2-495)
(2-496)
将式(2-494)~式(2-496)代入式(2-492)有:
(2-497)
因此,控制体积Vc1油液微分方程式(2-490)变为:
(2-498)
解上述微分方程式得:
(2-499)
利用初始条件Ts1(0)=T0,确定积分常数C。
所以
(2-500)
将式(2-500)代入式(2-499)有:
(2-501)
式(2-501)即是SPB泵控制体积Vc1的油液温度随时间的变化规律。同样可以表示为下列矩阵:
(2-502)
(2-503)
(4)结果分析
作出式(2-501)在直角坐标系下的图形,如图2-152所示。同样可求出最高温升幅值ΔTms1及温升速率KTs1。

图2-152 SPB泵控制体积Vc1的油温变化曲线
①最高温升幅度ΔTms1。
(2-504)
忽略斜盘及泵壳传热等影响有:
(2-505)
对控制体积Vc1应用连续性方程得:
(2-506)
得:
(2-507)
得:
(2-508)
有:
(2-509)
式(2-509)表明:由于泵自冷却流量ΔQc,自控制体积Vc2,经过控制体积Vc0,流向控制体积Vc1,因此,轴向柱塞泵存油容腔中油液总功率损失以油液温升形式体现于控制体积Vc1中,且与Vc1自冷却流量ΔQs1成正比。
②由温升速率KTs1可得到控制体积Vc1油液温升速率为:
(2-510)
由式(2-510)可求出任意时刻SPB泵控制体积Vc1的油液温升速率。
(三)结论
①SPB泵各控制体积的油液温度随时间增加呈负指数曲线,且单调增加,并存在一个极限温升幅值。
②由于SPB泵采用双盘配流原理,内部设有液流通道,能实现自冷却,因此,SPB泵控制体积油液最高温升幅值比CY泵明显降低,使SPB泵的主体在良好的冷却和润滑情况下运行。
通过以上理论分析,从理论上证明了开路式泵与闭路式泵在自冷却性能上的不同。
七、CY泵与SPB泵自冷却性能比较
根据柱塞泵内热量的产生方式及热量的传递形式,利用傅里叶定律和牛顿定律,建立柱塞泵泵腔内油液的微分方程,并求解得出油液温度的时变规律。
1.控制体积划分
将柱塞泵根据油液的存在状态以及摩擦副形式的不同划分为三段控制体积:斜盘滑靴段、泵壳缸体段、缸体配油盘段。根据能量守恒建立油液微分方程。在求解微分方程时,基于如下假设。
①工作介质(即油液)具有常物性,也就是说,油液密度ρ、黏度μ0、压力p、定压热容cp为常量,不随时间、空间、温度变化而变化。
②控制体积内油液热变换均匀,其温度仅是时间的函数,即θc=θc(t)。
③用温度平均值来描述控制体积油液温度,忽略其内部实际上存在的温度梯度。
2. CY泵各控制体积油温的时变规律
在控制体积V1内有生热元件,即斜盘滑靴副和缸体柱塞副,从控制体积V1中流出的泄漏油液流入控制体积V3中,根据能量守恒可得:
(2-511)
式中 E1——斜盘滑靴副泄漏油液产生的能量速率;
E2——缸体柱塞副泄漏油液产生的能量速率;
E3——斜盘滑靴副摩擦生热产生的能量速率;
E4——泵壳对流散热而损失的能量速率;
E5——流出控制体积V1的油液本身所具有的能量速率;
E6——其他损失掉的能量速率;
Ec1——控制体积V1内能的存储速率。
将斜盘看作一维平壁,将缸体、泵壳看作径向对称系统,求解各能量速率的具体表达式,可得:
(2-512)
(2-513)
(2-514)
式中 qV1——斜盘、滑靴间泄漏油液流量,L/min;
qV2——缸体、斜盘间泄漏油液流量,L/min;
qVc1——控制体积V1流出的油液流量,L/min;
θ1——斜盘、滑靴间泄漏油液温度, ℃;
θ2——缸体、斜盘间泄漏油液温度, ℃;
θc1——体积内油液任意时刻的温度, ℃;
θ∞——环境温度, ℃;
R31——斜盘总热阻;
R32——滑靴总热阻;
Rc1——泵壳Ⅰ段总热阻。
整理成标准形式并求解得:
(2-515)
同理可得:
(2-516)
(2-517)
SPB泵各控制体积的油温时变规律:
(2-518)
(2-519)
(2-520)
3.性能比较
(1)中高压工况下自冷却性能的比较
前面已经推导出了中高压工况下,CY泵和SPB泵存油容腔中油液温升的时变规律。为了便于对两种轴向柱塞泵进行准确的分析比较,这里假定SPB泵和CY泵规格相同,且工作在相同的使用环境、相同工况下。我们知道,油液温升以泵壳温升的形式显示出来,所以应首先从泵壳的外表面平均温度的最大值进行分析。根据参考文献可得:
(2-521)
式中 ——CY泵第i段最高温升幅度, ℃。
(2-522)
式中 ——CY泵第i段泵壳外表面最高温度, ℃;
——SPB泵第i段泵壳外表面最高温度, ℃;
θ0——t=0时刻油液温度, ℃;
Ryi——油液对第i段泵壳的对流热阻;
Rdi——第i段泵壳传导热阻;
Rki——空气对第i段泵壳的对流热阻;
Rzi——第i段泵壳总热阻。
与CY泵相比,SPB泵能够降低泵壳体内油液的温度,提高使用寿命,是因为SPB泵本身能够实现自冷却和自润滑。这一点可以从最高温升幅度Δθm表达式中一目了然。同时我们还可以求得两种泵各控制体积油液的最高温升幅度比。
(2-523)
对于同规格的SPB泵和CY泵,SPB泵自冷却流量远大于CY泵外泄漏流量,即因为,
,
。所以
,
,
。
同理推得:
因此,得到的结论是在中高压工况下SPB泵自冷却性能优于CY泵。
将两种泵同一控制体积的油液温升变化曲线在同一直角坐标下表示出来,如图2-153所示。

图2-153 CY泵与SPB泵油温对比
这说明,对同一控制体积CY泵的最高油温高于SPB泵。
(2)低压输出工况两种泵自冷却能力比较
所谓低压输出工况,是指当轴向柱塞泵出口压力ps与泵壳内油液压力p0之差Δp小于8MPa,使得各对摩擦副泄漏量很小,甚至为零时泵的工作状况。
低压输出工况分为两种情况。
Δp<8MPa,斜盘倾角β≠0时,称为低压大流量工况。
Δp<8MPa,斜盘倾角β→0时,称为低压小流量工况。
①低压大流量工况 对于CY泵,在低压大流量工况下时,虽然设有外部泄漏回油管路,但由于此时外部泄漏量ΔqV=0,泵壳与缸体之间的存油容腔中的油液被封闭。由于缸体的高速旋转,将产生黏性摩擦功率损失,并以存油容腔油液内能形式储存起来,表现为存油容腔油液温度急剧上升,这种现象称为自搅发热现象。
如果忽略泵壳体传热等损失,认为存油容腔内油液的黏性摩擦功率损失ΔW4全部转变成封闭油液的内能,并认为油液温度θc只与时间有关,则:
(2-524)
所以:
(2-525)
由式(2-525)可知,θc与t的关系是线性的,θc随时间呈直线上升。
事实上,自搅发热的现象自始至终存在于CY泵的每一个工况,只不过在其他工况,如Δp>8MPa时,油液存在泄漏现象,存油容腔中油液能够流动,故有一部分热量能够进行热传递,其温升随时间直线变化不明显。
对于SPB泵,由于采用开路式的自冷却、自润滑、双流道供油等方案,完全解决了低压大流量工况下的自搅发热问题。虽然在该工况下各摩擦副的泄漏量ΔqVs0=0,但是并不影响SPB泵的自冷流量ΔqVs0,也就是说,在该工况下,SPB泵各控制体积自冷却流量均为ΔqVs0,故仍能达到预期的冷却效果。
由以上分析可知,在低压大流量工况下,SPB泵完全优于CY泵。
②低压小流量工况 对于CY泵,在低压小流量工况时与低压大流量工况相同,将产生自搅发热现象。
对于SPB泵,当泵β≠0时,即在ΔqVs0=0时,泵则自冷却。也就是说,只要泵的qV,SPB泵就有进油,有进油就必然有一部分被分去参加泵的自冷却,使得容腔内油液温度不会随时间呈直线上升趋势。
需要指出的是,无论哪种泵,在β=0、ΔqV=0时都不能解决自搅发热问题。这时的前提条件是压力不高,或趋于零。
4.零流量输出工况自冷却性能的比较
这里所说的零流量输出工况,是指在轴向柱塞泵的输出压力ps与泵壳腔内油液的压力P0之差大于8MPa,而斜盘的倾角β→0时,即输出流量很小,甚至为零时泵的工作状态。
在这个工况下,如前所述,CY泵各种参数均与中高压工况相同,这时泄漏回油起一部分冷却作用,可以带走一部分热量,油液温度不会随时间呈直线上升趋势。但应当指出,对于整个泵来讲,它不是纯零流量。同时也相当于有一个与泄漏量相同的小泵在给这个泵进行冷却。
在这种工况下,SPB泵由于没有泄漏回油管路,且内部自冷却流量ΔqVs0=0,缸体与壳体内油液被封闭,产生自搅发热现象,泵壳温度随时间呈直线上升趋势。但是,这里需要指出,实际当中将泵如此使用是没有意义的,也就是说,在实际中泵不应工作在这种工况下。