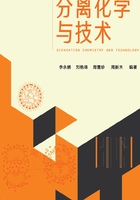
1.4 现代分离技术与新型分离技术的发展
现代工业中广泛应用了一些常规的分离技术,如蒸馏、吸收、萃取、吸附、结晶等。随着分离要求的不断提高,这些技术不断地得到改进和发展,成为现代分离技术中的主体。但我们会更加注意到一些各具特色的新颖分离过程和技术的出现和应用,如膜分离、泡沫分离、超临界流体萃取等等。这些新颖的分离技术,有的已在生产上得到一定规模的应用,但大多数还处于实验研究和工厂中试规模的开发阶段,但是这些方法都很有发展前途,而且各具特色,值得大家去重视、研究与发展。
新型分离技术是相对于传统分离技术而言的。新型分离技术的发展特点是通过多种技术的耦合来实现以局部的原始创新带动系统的集成创新。新型分离技术大致可分为三大类:
第一类为对传统分离过程或方法加以变革后的分离技术,如基于萃取分离的超临界萃取、液膜萃取、双水相萃取,基于吸附分离的色谱分离技术等。
第二类为基于材料科学的发展形成的分离技术,如反渗透、超过滤、气体分离以及渗透蒸发等膜分离技术。
第三类为分离材料与传统分离技术相结合形成的新型分离技术,如膜蒸馏、膜基吸收、膜基萃取、膜亲和超滤以及膜反应器等。
图1-3所示为以溶剂萃取、离子交换和膜分离技术为基础的,通过相互融合和发展派生出来的诸多新型分离技术。

图1-3 新型分离技术的衍生与拓展
溶剂萃取是一种已在工业生产中得到普遍应用的平衡级分离过程。该过程涉及水溶液或有机溶液中的组分被萃取进入另一不互溶的有机或水溶液中的过程。萃取是用于分离液体混合物的一种传统技术。早期的萃取分离方法是选择一种萃取剂,对混合物中待分离组分具有选择性溶解特性,而其余组分则不溶或少溶而获得分离。现代的萃取技术则侧重于利用萃取化学反应来改变物质在两相中的溶解度差别,进而使分离效果得到大大提高,应用范围也得到很大的拓展。因此,现代萃取分离技术在核燃料的提取、分离和纯化,化工、冶金、制药、生物、航天等工业领域得到广泛的应用。近30年来,基于某些新兴学科与技术的发展,又派生出了超临界萃取、双水相萃取、膜基萃取等新型萃取分离技术。与离子交换分离技术相结合,发展了萃淋树脂分离新技术,在超高纯稀土化合物的生产上起到了非常重要的作用。与膜分离技术相结合,发展了膜基萃取、液膜萃取等新技术,在人工肺和环境保护中得到了很好的应用。
1.4.1 基于传统分离方法的新型分离技术
1.4.1.1 基于萃取分离技术的新型分离技术
在生物制品和食品工业上,有机溶剂萃取常会使某些生物质失活,而且残留在药物及食品中的有机溶剂往往难以脱除,形成产品的污染。从20世纪60年代后期开始,系统研究开发了超临界萃取和双水相萃取等新型萃取过程。这些萃取技术中的萃取剂具有无毒性、易脱除、也容易保持生物活性等优点,很快在迅猛发展的生化、制药、食品等领域得到应用,并在应用中加深对其基础理论、设计、优化的研究。理论研究的深入又进一步扩大了这些技术的应用范围。超临界萃取具有节能、无污染、省资源、可在温和条件下完成分离操作等优点。近30年来,被用于石油、医药、食品、香料中许多特定组分的提取与分离,如从咖啡豆中脱除咖啡因,从啤酒花中提取有效成分,从油沙中提取汽油,从植物中提取某些有价值的生物活性物质(如药物、β-胡萝卜素、生物碱、香精香料、调味品和化妆用品等),植物和动物油脂的分级和有价值物质的提取、热敏物质的分离,高分子的聚合、分级、脱溶剂和脱挥发成分,有机水溶液的分离,含有机物的废水处理。此外,超临界萃取大多需在高压(10~100MPa)下进行。高压设备的费用常占工厂总投资一半以上,提高超临界萃取剂的溶解度和选择性、降低设备费用也是超临界萃取走向工业应用过程中应研究解决的重要内容。双水相萃取也是基于萃取机理的一种新型分离技术,20世纪60年代由瑞典学者Alberttson首先提出;70年代中期,联邦德国Kula等将双水相体系用于从细胞匀浆中提取酶和蛋白,改善了胞内酶的提取过程;目前还用于β-干扰素与杂蛋白的分离、废水中放射性元素的分离等,以及有关抗生素、氨基酸这类生物小分子分离的研究。
在环境保护领域的废水处理技术上,随着工业发展,废水、废气对环境的污染日益严重。一些排放量极大、浓度又低的物料,很难用常规分离方法进行处理。若用有机溶剂萃取含重金属离子的废水,溶剂与废水的比例高达1:10,且萃取后的分相和溶剂再生都很困难。为此,提出了液膜萃取技术。该技术以萃取技术为基础,但大大提高了传质比表面积,且可利用化学反应和载体促进传质,具有非常高的选择性和传质速率。1968年,美国Exxon公司黎念之首先提出了液膜分离技术,后来成功地应用于胶黏纤维工业废水中去除锌,尤其是支撑液膜技术在废水处理、湿法冶金、石油化工等领域得到重视和研究。液膜萃取集萃取和再生于一体,传质比表面积大,且可利用化学反应和载体促进传质,具有非常高的选择性和传质速度。例如,以NaOH为内相的乳化液膜进行含酚废水的脱酚,几分钟内即可将废水内酚含量降低到排放标准以下。因此在20世纪60年代液膜技术提出后,即在废水处理、湿法冶金、石油化工等领域得到重视和研究。
上述新型萃取过程与传统的溶剂萃取相比,主要差别是萃取剂或有机相组成改变了。但其基本原理、所用萃取设备及过程的计算、设计方法等与溶剂萃取基本相似。从原理上说,都是利用组分在两相的分配差进行分离。从分离用设备看,都可以用填料塔、筛板塔等塔式传质设备,也都可以用简单的混合澄清槽进行萃取和分相,设备高度也可通过传质单元数、传质单元高度或理论板的计算得到。但由于所用萃取剂及被萃取组分物理化学性质上的差异,因此塔内的流体力学和传质性能各有其独特处,需要对这些新型萃取过程传质设备内的流体力学和传质性能进行研究。一种新技术能否用于实际生产,除与该技术对目的产物的分离、提纯能力有关外,还取决于分离的速度,后者决定了过程的经济性和实际可行性。分离速度当然取决于设备的传质性能,因此对这些新型萃取过程传质及流体力学性能的研究,是当前这些新型萃取技术从实验研究走向工业生产的关键之一。而这些模型的建立,需要密度、黏度、界面张力、扩散系数、分配系数等物理量及其关联式,因此必须同时加强对这些新体系基础数据测定和关联的研究工作。
1.4.1.2 基于色谱分离技术的新型分离技术
色谱分离技术基于传统的吸附平衡机理,利用组分在固定相上和流动相内的分配平衡差异进行分离的。吸附色谱的分离原理与吸附分离相似,而分配色谱则与精馏相似。色谱比吸收及精馏有高得多的分离效率是由于流动相和固定相之间不断的接触平衡所造成的。装填好的色谱柱可从几百到上千的平衡级,特别适用于精馏等过程难以分离体系的分离。
目前工业规模色谱主要应用于三方面:一是以模拟移动床形式进行分离操作的固液吸附色谱,通称Sorbex过程,所用柱填料多为合成沸石分子筛,分离对象是二甲苯异构体、油品脱蜡、果糖-葡萄糖分离等多个体系;二是生化产品分离的吸附色谱及凝胶色谱;三是用于香料等提取的气液分配色谱。
对色谱分离的研究和传质模型的建立,以前大多是对线性色谱进行的,而用于工业规模分离的色谱多为非线性色谱,对非线性色谱虽也提出过许多传质模型,但到目前为止尚无法对建立的模型求得一般的数学解,因此难以指导过程的优化和放大,这也是色谱技术迟迟难以从分析规模进入工业规模分离应用的原因之一。目前常从化学工程的角度出发,对影响放大的各因素进行定性分析,以指导色谱过程的优化和放大。就目前的状况看,要通过传质模型进行非线性色谱的优化和放大还有很大差距,对非线性色谱还必须加强理论研究。
1.4.1.3 基于蒸馏等分离技术的新型分离技术
分子蒸馏又称短程蒸馏,是在高真空(一般为10-4Pa数量级)下进行的蒸馏过程,其蒸发面和冷凝面的间距小于或等于被分离物蒸气分子的平均自由程,由蒸发面逸出的分子相互间无碰撞、无阻拦地喷射到冷凝面并在其上冷凝,在这种特殊的传质条件下分子蒸馏的蒸发速率可高达20~40g/(m2·s)。分子蒸馏具有温度低、受热时间短、分离程度高等特点,适合于浓缩、纯化或分离高分子量、高沸点、高黏度及热稳定性差、易氧化的物料。
泡沫分离和磁分离技术早就在选矿中应用,目前其分离范围从不溶性固体扩展到可溶解性组分,从分离单纯的表面活性物质,扩大到金属离子等非表面活性物质。因其设备简单,处理容量大,又特别适合溶液中低浓度组分的分离、回收,非常适合某些工业废水中重金属离子的脱除。如冶金与原子能工业废水的处理,照相、电镀和宝石生产废水中回收有价值组分。
泡沫分馏的操作及所用设备与精馏过程很相似,但泡沫分离是利用组分在气液界面即气泡上的选择吸附进行分离的过程,是表面化学的一种成功应用。泡沫是一多相非均匀体系,影响泡沫分离的因素极其复杂,早期的研究多为定性分析,随着电子计算机的应用,过程的动力学及数学模型的研究有了很大进展。
1.4.2 基于材料科学的发展形成的分离技术——膜分离技术
随着科学技术的发展,人们模仿生物膜的某些功能,制备出各种合成膜,并开拓出相应的膜技术应用于日常生活与生产过程中。由于膜与膜技术的应用范围不断扩大,因此,它的应用价值与重要性也逐渐被人们所认识。
膜分离技术是利用膜对混合物各组分选择渗透性能的差异来实现分离、提纯或浓缩的新型分离技术。组分通过膜的渗透能力取决于分子本身的大小与形状,分子的物理、化学性质,分离膜的物理化学性质以及渗透组分与分离膜的相互作用。由于渗透速率取决于体系的许多性质,这就使膜分离与只取决于较少物性差别的其他分离方法相比,具有极好的分离能力。
膜分离技术的主体是膜,而膜涉及多个学科,因此在膜的分类上也不统一,但概括起来大致可按膜的性质、结构、材料、功能及作用机理等分为五大类。在化工过程中,通常为具有分离或反应功能的合成膜,这类膜可按作用机理、推动力及膜组件结构细分。
按作用机理可分为有孔膜的筛分机理、无孔膜的溶解扩散机理、活性基团的反应或亲和吸附机理等;按推动力可分为压力差、浓度差、电位差、温度差等;按膜组件结构可分为板框(盒)式、螺旋卷式、中空纤维式、管式四大类。由于膜的种类很多,除了用于分离的膜外,还有用于分子识别、能量转换、电光转换等的功能膜。
另外还有两类正在开发与推广应用的新型膜技术:
一类目前称为膜接触器,包括膜基吸收、膜基萃取、膜蒸馏、膜基汽提等。在这些过程中,膜介质本身对待处理的混合物无分离作用,主要利用膜的多孔性、亲水性或疏水性,为两相传递提供较大而稳定的相接触面,可克服常规分离中的液泛、返混等影响,因而近十余年来,深受化工界的关注。
另一类是以膜为关键技术的集成分离过程,包括膜与蒸馏、膜与吸附、膜与反应等相结合的集成过程,具有常规分离过程所不能及的优点,也正在受到重视和发展。随着科学技术的发展,人们模仿生物膜的某些功能,研制出各种功能的合成膜,应用于日常生活与工业生产过程中。可以认为,膜产业将成为21世纪初发展最快的高新技术产业。
1.4.3 基于多种分离方法耦合与集成的新型分离技术
多数分离过程都是由多个分离单元操作构成的。也就是说单纯依靠一种技术或一个单元操作是很难达到高效分离目的的。要取得效果更好,也更经济的分离,多种分离方法的耦合和集成是主要的发展方向。集成过程的最大特点是:实现物料与能量消耗的最小化、工艺过程效率的最大化,或为达到清洁生产目的,或为实现混合物的最优分离和获得最佳的产物浓度。
(1)传统分离与膜分离集成技术
膜分离技术与常规的反应或分离方法相耦合的集成技术。如膜分离分别与蒸馏、吸收、萃取等常规化工分离技术相结合,以使分离过程在最佳条件下进行;膜分离与化学反应相结合,能在反应的同时不断移去过程中的生成物,使反应不受平衡的限制,以提高反应转化率。采用这种集成技术比单独应用膜分离技术更有效、更经济。
①精馏-渗透汽化集成技术:采用亲水性渗透汽化膜与常规的精馏过程集成可将醇-水混合物中的水脱除,得到无水醇。该集成工艺过程中不会带入萃取剂或恒沸剂,可使产物杂质降低。以此醇类产品作食品或药物溶剂,则最终产品也可认为是安全的。渗透汽化与汽提集成生产无水乙醇试剂,乙醇的损失几乎为零,没有环境污染。
②渗透汽化-萃取集成技术:从有机物水溶液中萃取有机物或污水中除去有机毒物,常用亲水和亲有机物渗透汽膜与萃取结合过程,如利用水-甲基乙基酮(MEK)体系的溶解度特性,水溶液层(底部)含23%(质量分数)MEK,富有机物层(上层)含89%(质量分数)MEK,从水溶液中回收MEK,其纯度可达到99%。
③错流过滤和蒸发集成技术:一般润滑油不能用于低温,因其中含蜡易固化,因此,石油炼制中常用溶剂来脱除原料中的蜡,再冷却,将沉淀的蜡滤去,除蜡后的溶剂用蒸馏法回收,其能耗很大,是整个工艺过程中最主要的部分。1998年5月Mobil炼油厂采用膜技术与蒸馏法结合,先用错流过滤分离至少50%的溶剂,然后用蒸馏法处理。提高润滑油产率25%(体积分数),运行成本为常用技术的1/3。
④膜渗透与变压吸附集成技术:商业上所选用的膜,其O2/N2分离系数在3.5~5,富氧浓度为30%~45%,而氮浓度不高。若以氧富集为目的,在低流率、低浓度时,膜法有利;对于超纯氮的生产,以变压吸附(PSA)有利。以膜法和PSA结合的集成工艺在大规模高纯氮生产中具有较大的竞争力,特别对生产35%的O2和95%以上的N2时,比较经济。
(2)反应-分离耦合集成技术
在化学反应中,常由于产物的生成而抑制反应过程的进行,甚至导致反应的停止。及时将产物(副产物)移出,可促进反应的进一步进行,提高转化率,采用反应-分离集成技术具有十分重要的意义。
①催化反应-蒸馏集成技术:反应蒸馏是化学反应和蒸馏结合的新型分离技术,其过程可在同一个蒸馏设备内实现。与反应、蒸馏分别进行的传统方法相比,具有投资少、流程简单、节能、产品收率高等优点。反应蒸馏的一般性规律始于20世纪60年代末,后来扩大到非均相反应,特别是通过有关反应蒸馏的计算数学模拟研究,促进了反应蒸馏过程的开发。
②酯化反应-渗透汽化集成技术:渗透汽化与酯化反应相结合,可以利用渗透汽化亲水膜移去酯化反应过程中产生的水分,促使反应向酯化方向进行,提高转化率,也提高转化速率,节省能耗。近年来已有较多体系被工业开发或采用,例如二甲脲(DMU)生产中,以合成反应辅助以渗透汽化分离器,过程中可移去水,回收并循环使用甲胺和CO2,使转化率提高,生产费用降低。
③膜基化学吸收集成技术:天然气中的CO2、H2S和水汽含量一般很高,为防止输运管道腐蚀和冻结堵塞,需将其及时除去。采用膜基化学吸收可很快渗透除去碳氢化合物混合气中的酸性气体,且无环境污染和防火问题,其投资费用较低,可在井头上处理,避免送料管路的腐蚀和不安全问题。