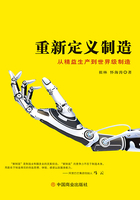
二、世界级制造的理论起源
300年来,人类的制造技术取得了巨大的发展。18世纪中叶从手工作业到动力技术的突破开启了人类社会的工业化,机械化加电气化技术催生了人类制造业;20世纪的机械技术、机电自动化技术,以及随之出现的大批量生产模式(见图2-1)、机械制造业成形,加速了制造业的发展;从1946年电子计算机问世到20世纪80年代后期,以计算机辅助制造(Computer Aided Manufacturing)为标志的第一波自动化制造达到顶峰;数字化技术出现之后,人类社会掀起了第二波自动化浪潮,随着互联网(Internet)和信息技术(Information Technology)的发展和融入,美国联邦政府于2013年推出了先进制造技术(Advanced Manufacturing Technology)计划,极大地推动了制造技术的突破,随着物联网(Internet of Things)技术、人工智能(Artificial Intelligence)和云计算(Cloud Computing)技术等突飞猛进,制造业的形态随之发生巨大变化,先进制造业(Advanced Manufacturing)渐露雏形,智慧工厂、智能化制造逐步清晰。

图2-1 制造技术300年发展历程
伴随制造技术的发展,制造业的管理技术、理论和模式也开始进化(见图2-2)。

图2-2 制造管理百余年发展历程
19世纪80年代,美国学者泰勒(Frederick W.Taylor)和吉尔布雷斯(Frank B.Gilbreth)从动作分析和方法改善着手,开创了工业工程(Industrial Engineering)的先河,1908年福特公司第一条流水线生产,标志着工业工程的诞生;20世纪20年代,美国企业开始把统计抽样应用于预见性的质量管理,统计技术(Statistical Techniques)逐步发展为三大管理技术(IE、VE和ST)之一;1947年,美国通用电气(GE)采购主管迈尔斯发表了名为《价值分析(Value Analysis)》的文章,开启了价值工程(Value Engineering)这一技术和学科。
20世纪50年代,通用电气质量专家阿曼德·费根堡姆(Armand Vallin Feigenbaum)提出全面质量管理理论(Total Quality Management)。60年代初,美国管理大师菲利浦·克劳士比(Philip Crosby)提出零缺陷管理理论(Zero Defect),1965年英国的Molins公司提出柔性生产概念(Flexible Production)。随着日本在第二次世界大战之后的经济崛起,以准时制生产(Just In Time)为目标的丰田生产方式(Toyota Production System)在全球制造业创造了非常大的竞争优势,在美国市场对美国企业造成了巨大冲击。80年代中期,全球开始推行质量体系认证(ISO)。1998年,美国摩托罗拉公司和通用电气公司的六西格玛(6Q)质量管理模式成形。
自20世纪80年代初期开始,美国和日本进行了长达十多年的贸易战,同时,美国官产学各界对日本模式进行了十多年的全面深入研究,据此提出了一系列的管理理论,作为再造美国产业竞争力的强大指引。1984年,艾利·高德拉特(Eliyahu M.Goldratt)提出了约束理论(Theory of Constraints,也称“瓶颈理论”)。1985年,美国学界提出了从纵向一体化向横向一体化转变的供应链管理思想,逐步发展为供应链管理(Supply Chain Management)理论。1986年,世界级制造思想(World-class manufacturing ideas)横空出世。1990年,美国麻省理工学院的国际汽车研究项目发表成果报告,在其出版的《改变世界的机器》一书中提出了精益生产理论(Lean Production)。1993年,美国联邦政府启动全面超越日本、在全新层次创造美国产业优势的先进制造技术(Advanced Manufacturing Technology)计划。
“世界级制造”是由美国学者理查德·施恩伯(Richard Schonberger)在1986年首创的一个术语,是在研究丰田生产方式之后提出一整套企业运营管理的思想、方法和工具体系。
1.“世界级制造”的提出
20世纪70年代到80年代,由于美国经济受到日本冲击,工业霸主地位不复存在。从80年代到90年代,美国研究和效仿日本制造技术并创新,提出了三大理论:一是最彻底的革命理论,即业务流程再造(Business Process Re-engineering, BPR);二是持续渐进的改善体系,即精益生产(Lean Production, LP);三是着眼于世界级水准的系统能力建设,即世界级制造(World Class Manufacturing, WCM)。
美国华盛顿州立大学教授理查德·施恩伯最早研究日本经济崛起经验,从20世纪80年代到21世纪初,二十多年中一直是先进制造理论最敏锐的先知、新管理方法的开路先锋。1982年,他发表《日本制造技术:简化技术的9项秘诀》(Japanese Manufacturing Technology:Nine Hidden Lessons In Simplicity),这是西方最早全面介绍日本成功经验的著作。1986年,施恩伯教授发表了《世界级制造I:简化技术应用的经验》(World Class Manufacturing I:The Lessons of Simplicity Applied)的著作,创造了“世界级制造”的术语和概念。这两部著作实际上是一个内容:介绍和推广日本的制造技术——当时他称之为“简化技术”(simplicity)。他将当时的日本生产方式定位为“世界级制造”,成功实施日本简化技术的企业是“世界级制造企业”。1987年,他又发表了《世界级制造案例:实施JIT和TQC》(World Class Manufacturing Casebook: Implementing JIT and TQC),主要对实现世界级的方法进行补充。十年之后的1996年,他的又一部世界级著作《世界级制造Ⅲ:今后十年》(World Class ManufacturingIII: The Next Decade)问世,从而铸就了施恩伯“世界级制造”的基础理论。
施恩伯教授认为,日本成功的动力是以准时生产(JIT)和全面质量管理(TQC)为核心的简化(或称“合理化”)技术:实行JIT和解决过量库存问题,TQC和企业的持续改进,生产过程的简化,使产品像水一样流动、简化工厂的结构——打破部门之间的壁垒,生产设施柔性化,职工参与,等等。他对日本制造技术的认知为他提出世界级制造理论提供了重要的思想原则和方法,是向“世界级制造”概念迈出的第一步。依据世界级企业准则,按照准则矩阵要求规划自己的改进步骤,走精益的道路,持续不断地改进,最终达到世界级水平的高境界,从而使企业成为“世界级制造”。
世界级制造企业是对客户高水平服务的组织,能够快速灵活地响应客户的需求,为客户提供质量更好、价格更便宜的产品和服务,并且能够持续不断地改进这些能力。
2.世界级制造与精益生产同根同源
世界级制造与精益生产是同根同源的关系,它们之间是有内在联系的:客户立场和持续改进是它们的共同特征,简化技术是二者共同重视的“因”(方法),精益是其“果”(目标);而世界级制造则站在世界级水准的高度看待精益追求的更高境界。
在客户立场方面,精益生产以客户的观点定义价值,用客户需求拉动价值流。世界级制造认为:判断企业成功的两个根本是库存周转和客户满意度。“财务数据并不是评价企业经营状态的最好的指标,而诸如库存周转率、客户满意度等基本指标会更加有效”,这是世界级制造评价企业是否健康和成功的关键因素。测量客户满意度的指标则是客户最敏感的四项要素:QSFV。其中,Q指的是Quality,代表质量;S指的是Speedy Response,代表响应速度;F指的是Flexibility,代表柔性;V指的是Value,代表价值。
在持续改进方面,精益生产通过持续不断的改善朝着尽善尽美的方向前进,小步快跑的改进方式是精益的特征之一,世界级制造强调更快、更高、更强,重视持续和及时的改进。世界级制造成为组织和激励企业永不满足和不断进步的概念,而不是某项“世界第一”的现状,这是理解世界级制造概念的关键。
3.世界级制造推动世界制造业的进步和发展
世界级制造体系包括一组以JIT和TQC为主的简化技术、库存周转分析和持续快速改进等改造传统管理模式的理论和方法;一套引导企业管理进步的准则矩阵;大量基于制造业最佳实践的标杆数据和一套企业业绩测评方法。其要点可概括为:(1)客户至上、持续和快速改进;(2)一套为世界著名企业共同追求的世界级企业评估标准;(3)企业对自己进步的测评和鞭策,而非谁是第一、第二;(4)作为同类先进管理理论特别是精益思想的汇总应用;(5)WCM理论正在不断发展,正走向与精益融合的新阶段。
实际上,日本制造业对美国经济造成巨大冲击后,有关日本企业运营的优势研究有两大成果:一是精益生产,二是世界级制造。
由于精益生产的理论体系成形于1990年,而世界级制造虽然早于精益生产提出,但它的理论体系一直到1996年才基本成形,所以,相对于世界级制造,精益生产在全球的传播和推广要更广泛。
近20年来,WCM对北美和欧洲企业的复兴和繁荣起着重要的作用,最近又瞄准了发展中国家的企业在进步中的问题,推动着世界制造业的进步和发展。