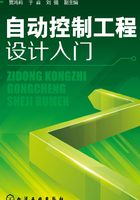
第一节 控制方案的确定
一、控制方案的确定
进行生产过程的自控设计,首先要了解生产工艺过程的构成及特点。
石油化工生产过程的构成可由图3-1概括。

图3-1 石油化工生产过程的构成
石油化工生产过程的主体,一般是化学反应过程。化学反应过程中所需的加工原料,首先送入输入设备。然后将原料送入前处理过程,对原料进行分离或精制,使它符合化学反应对原料提出的要求和规格。化学反应后的生成物进入后处理过程,在此将半成品提纯为合格的产品并回收未反应的原料和副产品,然后进入输出设备中储存。同时为了化学反应及前、后处理过程的需要,还有从外部提供必要的水、电、汽以及冷量等能源的公用工程。现代大多还有能量回收和三废处理系统等附加工程。
石油化工生产过程的特点是产品从原料加工到成品完成,流程都较长而复杂,并伴有副反应。工艺内部各变量间关系复杂,操作要求高。关键设备停车会影响全厂生产。大多数物料是以液体或气体状态在密闭的管道、反应器、塔与热交换器等内部进行各种反应、传质、传热过程。这些过程经常在高温、高压、易爆、易燃、有毒、有腐蚀、有刺激性臭味等条件下进行。
控制方案的正确确定应当在与工艺人员共同研究的基础上进行。要把自控设计提到一个较高水平,自控设计人员必须熟悉工艺,这包括了解生产过程的机理,掌握工艺的操作条件和物料的性质等。然后才能应用控制理论结合工艺情况确定所需的控制点,并决定整个工艺流程的控制方案。控制方案的确定主要包含以下几方面的内容:
①根据工艺要求,确定被调参数和调节参数,组成自动控制(调节)系统;
②确定所有的检测点及安装位置;
③生产安全保护系统的建立,包括声、光信号报警系统、联锁保护系统及其他保护性系统的设计。
二、在控制方案的确定中应处理好的几个关系
(一)可靠性与先进性的关系
在控制方案确定时,首先应考虑到它的可靠性,否则设计的控制方案不能被投运、付诸实践,将会造成很大的损失。在设计过程中,将会有两类情况出现,一类是设计的工艺过程已有相同或类似的装置在生产运转中,此时,设计人员只要深入现场进行调查研究,吸取现场成功的经验与原设计中不足的教训,其设计的可靠性是较易保证的;另一类是设计新的生产过程,则必须熟悉工艺,掌握控制对象,分析扰动因素,并在与工艺人员密切配合下确定合理的控制方案。
可靠性是一个设计成败的关键因素。但是从发展的眼光来看,要推动生产过程的自动化水平不断前进,先进性将是衡量设计水平的另一个重要标准。
先进性在很大程度上取决于仪表的选型,要从发展的角度看准那些有发展前景的、先进的、甚至超前的仪表。由于一个大的工程从设计到投产需要几年的时间,仪表选型过于保守,到投产之时仪表已经落后、淘汰。这也是一种浪费、损失。
当前,在设计工作中似乎已形成一个规矩:采用的方案必须是有依据的,经过实践检验是有效和成熟的。这样在某个生产过程中行之有效的先进控制方案,对于另一个生产过程来说,由于处理的介质不同,或者处理量的不同,推广应用也就成了问题。例如已很成熟的前馈控制系统,国内20世纪50~70年代的许多研究试验表明,它与一般反馈系统相比具有许多长处,但在设计中采用的还是不多。所以在考虑自控方案时,必须处理好可靠性与先进性之间的关系,一般来说,可以采用以下两种方法。
一种是留有余地,为下一步的提高水平创造好条件。也就是在眼前设计时要为将来的提高留好后路,不要造成困难。
另一种是作出几种设计方案,可以先投运简单方案,再投运下一步的方案。采用集散系统及数字调节器时,完全可以通过软件来改变方案。
(二)自控与工艺、设备的关系
要使自控方案切实可行,自控设计人员熟悉工艺,并与工艺人员密切配合是必不可少的。然而,目前大多数是先定工艺,再确定设备,最后配自控系统。由工艺方面来决定自控方案,而自动化方面的考虑不能影响到工艺设计的做法,是目前国内普遍采用的方法。自控人员长期处于被动状态并不是正常现象,相反在国外工艺、设备与自控三者的整体优化是现代石油化工工程设计的标志,这是大系统要解决的问题。
(三)技术与经济的关系
设计工作除了要在技术上可靠、先进外,还必须考虑经济上的合理性。所以在设计过程中应在深入实际调查的基础上,进行方案的技术、经济比较。
处理好技术与经济的关系。要看到自控水平的提高将会增加仪表部分的投资,但可能从改变操作、节省设备投资或生产效益、节省能源等方面得到补偿。但又要看到,自控方案越复杂,采用的仪表越先进,并不一定是自动化水平就越高。盲目追求而无实效的做法,不代表技术的先进,而只能造成经济上的损失。此外,自动化水平的高低也应从工程实际出发,对于不同规模和类型的工程,作出相应的选择,使技术和经济得到辨证的统一。