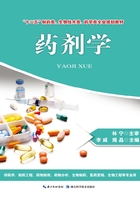
第四节 空气净化技术
空气净化系指以创造洁净空气为目的的空气调节措施。根据不同行业的要求和洁净标准,可分为工业净化和生物净化。空气净化技术系指为达到某种净化要求所采用的净化方法。工业净化系指除去空气中悬浮的尘埃粒子,以创造洁净的空气环境,如电子工业等。在某些特殊环境中,可能还有除臭、增加空气负离子等要求。生物净化系指不仅除去空气中悬浮的尘埃粒子,而且要求除去微生物等以创造洁净的空气环境。如制药工业、生物学实验室、医院手术室等均需要生物洁净。空气净化技术是一项综合性技术,该技术不仅着重采用合理的空气净化方法,而且必须对建筑、设备、工艺等采用相应的措施和严格的维护管理。
一、注射剂车间的基本要求
注射剂生产,要求洁净的生产环境,这取决于注射剂的车间设计及生产过程的管理。
(一)设计要求
注射剂车间的设计是一种综合性的建筑物设计,需对房间布局、管道、下水道、通风、照明,空气净化及设备安装等作系统的考虑。
1.位置选择 注射剂车间应选择空气洁净的地方,远离灰尘量大的马路烟囱等。周围环境应安静、开阔、光线充足,无泥土外露,可种植草坪,但不能种花。
2.房间布局 首先房间应按照注射剂的生产工艺流程及所要求的洁净度级别合理布局,如注射剂车间按工序一般划分为洗涤室、配滤室、灌封室、灭菌室、质检室等,工序之间应相互衔接,同时人流、物流应严格分开;其次根据各工序对洁净度的要求不同,将注射剂车间按洁净度划分为一般生产区、控制区及洁净区,各区域的洁净度标准及适用范围见空气净化技术的表3-2及表3-3。
表3-2 《药品生产质量管理规范》中洁净度标准

表3-3 各种注射剂及工序对洁净度的要求

3.内部结构 室内的电气线路,抽气管道应全部嵌入墙内,内表面应平整光滑、无缝隙、接口严密、无颗粒脱落,并能耐受清洗与消毒。墙壁与天棚及地板连接处应砌成弧形或采取其他措施,以减少灰尘积聚和便于清洗。
(二)车间管理
1.生产工艺规程 其内容包括品名、剂型、处方、生产工艺的操作要求,物料、中间产品、成品的质量标准、技术参数及贮存事项,成品容器、包装材料的要求等。
2.批生产记录 系指一个批次的成品的所有生产记录,以提供该批产品的生产历史以及与质量有关的情况。注射剂及其他制剂生产记录的具体形式参看《GMP实施细则》。
3.洁净室的管理 洁净室是注射剂车间的核心及注射剂生产的关键部位,因此,对洁净室的管理就显得非常重要。
二、洁净室的净化标准与测定方法
(一)洁净室空气净化标准
1.含尘浓度 即单位体积空气中所含粉尘的个数(计数浓度)或毫克量(重量浓度)。
2.净化方法 常见的可分为三大类。
(1)一般净化 以温度、湿度为主要指标的空气调节,可采用初效过滤器。
(2)中等净化 除对温度、湿度有要求外,对含尘量和尘埃粒子也有一定指标(如允许含尘量为0.1 5~0.25mg/m2,尘埃粒子不得≥1.0μm)。可采用初、中效二级过滤。
(3)超净净化 除对温、湿度有要求外,对含尘量和尘埃粒子有严格要求,含尘量采用计数浓度。该类空气净化必须经过初、中、高效过滤器才能满足要求。
3.洁净室的净化度标准 目前世界各国在净化度标准方面尚未统一。我国《药品生产管理规范》中净化度标准见表3-2。从表3-2可知,洁净室必须保持正压,即按洁净度等级的高低依次相连,并有相应的压差,以防止低级洁净室的空气逆流至高级洁净室中。除有特殊要求外,我国洁净室要求:室温为18~26℃,相对湿度为40%~60%。
(二)浮尘浓度测定方法和无菌检查法
1.浮尘浓度测定方法 测定空气中浮尘浓度和粒子大小的常用方法有:光散射法、滤膜显微镜法和比色法。
(1)光散射式粒子计数法 当含尘气流以细流束通过强光照射的测量区时,空气中的每个尘粒发生光散射,形成光脉冲信号,并转化为相应的电脉冲信号。根据散射光的强度与尘粒表面积成正比,脉冲信号次数与尘粒个数相对应,最后由数码管显示粒径和粒子数目。
(2)滤膜显微镜计数法 采用微孔滤膜真空过滤含尘空气,捕集尘粒于微孔滤膜表面,用丙酮蒸气熏蒸至滤膜呈透明状,置显微镜下计数。根据空气采样量和粒子数计算含尘量。该法可直接观察尘埃的形状、大小、色泽等物理性质,这对分析尘埃来源及污染途径具有较高的价值,但取样、计数较繁琐。
(3)光电比色计数法 采用滤纸真空过滤含尘空气,捕集尘粒于滤纸表面,测定过滤前后的透光度。根据透光度与积尘量成反比(假设尘埃的成分、大小和分布相同),计算含尘量。常用于中、高效过滤器的渗漏检查。
2.无菌检查法 系指检查药品与辅料是否无菌的方法,是评价无菌产品质量必须进行的检测项目。无菌制剂必须经过无菌检查法检验,证实已无微生物生存后,才能使用。《中国药典》规定的无菌检查法有“直接接种法”和“薄膜过滤法”。
(1)直接接种法 将供试品溶液接种于培养基上,培养数日后观察培养基上是否出现混浊或沉淀,与阳性和阴性对照品比较或直接用显微镜观察。
(2)薄膜过滤法 取规定量供试品经薄膜过滤器过滤后,取出滤膜在培养基上培养数日,观察结果,并进行阴性和阳性对照试验。该方法可过滤较大量的样品,检测灵敏度高,结果较“直接接种法”可靠,不易出现“假阴性”结果。但应严格控制过滤过程中的无菌条件,防止环境微生物污染而影响检测结果。
三、空气过滤
空气过滤是洁净室的空气净化一般常用的方法,当含尘空气通过多孔过滤介质时,粉尘被微孔截留或孔壁吸附,达到与空气分离的目的。该方法是空气净化中经济有效的关键措施之一。
(一)过滤方式
空气过滤属于介质过滤,可分为表面过滤和深层过滤。
1.表面过滤 系指大于过滤介质微孔的粒子截留在介质表面,使其与空气得到分离的方法。常用的过滤介质有醋酸纤维素、硝酸纤维素等微孔滤膜。主要用于无尘、无菌洁净室等高标准空气的末端过滤。
2.深层过滤 系指小于过滤介质微孔的粒子吸附在介质内部,使其与空气得到分离。常用的介质材料有:玻璃纤维、天然纤维、合成纤维、粒状活性炭、发泡性滤材等。
(二)空气过滤机理及影响因素
1.空气过滤机理 按尘粒与过滤介质的作用方式,可将空气过滤机理大体分为拦截作用和吸附作用。
(1)拦截作用 系指当粒径大于纤维间的间隙时,由于介质微孔的机械屏障作用截留尘粒,属于表面过滤。
(2)吸附作用 系指当粒径小于纤维间隙的细小粒子通过介质微孔时,由于尘埃粒子的重力、分子间范德华力、静电、粒子运动惯性及扩散等作用,与纤维表面接触被吸附,属于深层过滤。
2.空气过滤的主要影响因素
(1)粒径 粒径愈大,拦截、惯性、重力沉降作用愈大,愈易除去;反之,愈难除去。
(2)过滤风速 在一定范围内,风速愈大,粒子惯性作用愈大,吸附作用增强,扩散作用降低,但过强的风速易将附着于纤维的细小尘埃吹出,造成二次污染,因此风速应适宜;风速愈小,扩散作用愈强,小粒子愈易与纤维接触而吸附,常用极小风速捕集微小尘粒。
(3)介质纤维直径和密实性 纤维愈细、愈密实,拦截和惯性作用愈强,但阻力增加,扩散作用减弱。
(4)附尘 随着过滤的进行,纤维表面沉积的尘粒增加,拦截作用提高,但阻力增加,当达到一定程度时,尘粒在风速的作用下,可能再次飞散进入空气中,因此过滤器应定期清洗,以保证空气质量。
(三)常用的空气过滤器
空气过滤器常以单元形式制成,即将滤材装入金属或木质框架内组成一个单元过滤器,再将一个或多个单元过滤器安装到通风管道或空气过滤箱内,组成空气过滤系统。单元过滤器一般可分为:板式、契式、袋式和折叠式空气过滤器(图3-9)。

图3-9 各种空气过滤器示意图
1.板式滤过器;2.契式滤过器;3.袋式滤过器;4.折叠式滤过器
1.板式空气过滤器 是最常用的初效过滤器,亦称预过滤器。通常置于上风侧的新风过滤,主要滤除粒径大于5μm的浮尘,且有延长中、高效过滤器寿命的作用。
2.契式和袋式空气过滤器 用于中效过滤,两种空气过滤器的外形、结构相似,仅滤材不同,主要用于滤除大于1μm的浮尘,一般置于高效过滤器之前。
3.折叠式空气过滤器 由于滤材折叠装置,减小了通过滤材的有效风速,对微米级尘粒捕集效率高,用于高效过滤,主要滤除小于1μm的浮尘,对粒径0.3μm的尘粒的过滤效率在99.97%以上,一般装于通风系统的末端,必须在中效过滤器保护下使用。其特点是效率高、阻力大、不能再生、有方向性(正反方向不能倒装)。
四、洁净室(区)的设计
制药企业应按照药品生产种类、剂型、生产工艺和要求等,将生产厂区合理划分区域。通常可分为一般生产区、控制区、洁净区和无菌区。根据GMP设计要求,一般生产区无洁净度要求;控制区的洁净度要求为10万级;洁净区的洁净度要求为1万级(亦称一般无菌工作区);无菌区的洁净度要求为100级。
(一)洁净区基本布局
洁净区一般由洁净室、风淋、缓冲室、更衣室、洗澡室和厕所等区域构成(如图3-10所示)。各区域的连接必须在符合生产工艺的前提下,明确人流、物流和空气流的流向(洁净度从高到低),确保洁净室内的洁净度要求。基本原则是:洁净室面积应合理,室内设备布局尽量紧凑,尽量减少面积;同级别洁净室尽可能相邻;不同级别的洁净室由低级向高级安排,彼此相连的房间之间应设隔离门,门应向洁净度高的方向开启,各级洁净室之间的正压差一般设计在10Pa左右;洁净室内一般不设窗户,若需窗户,应以封闭式外走廊隔离窗户和洁净室;洁净室门应密闭,人、物进出口处装有气阀;光照度应大于300Lx;无菌区紫外灯一般安装在无菌工作区上方或入口处。

图3-10 洁净室平面示意图
1.洁净室;2.走廊;3.凤淋(气闸);4.非污染区;5.亚污染区;6.厕所;7.水洗;8.休息室;9.擦脚;10.管理室;11.更衣;12.气阀;13.进口;14.出口
(二)洁净室对人员、物件及内部结构的要求
洁净室的设计方案、所用材料是保证洁净室洁净度的基础,但洁净室的维护和管理同样重要。一般认为,设备和管理不善造成的污染各占50%。
1.人员要求 人员是洁净室粉尘和细菌的主要污染源。如人体皮屑、唾液、头发、纤维等污染物质。为了减少人员污染,操作人员进入洁净室之前,必须水洗(洗手、洗脸、淋浴等),更换衣、鞋、帽,风淋。服饰应专用,头发不得外露,尽量减少皮肤外露;衣料采用发尘少、不易吸附、不易脱落的紧密尼龙、涤纶等化纤织物。
2.物件要求 物件包括原料、仪器、设备等,这些物件在进入洁净室前均需洁净处理。长期置于洁净室内的物件应定时净化处理,流动性物料一般按一次通过方式,边灭菌边送入无菌室内。如安瓿和输液瓶经洗涤、干燥、灭菌后,采用输送带将灭菌容器经洁净区隔墙的传递窗送入无菌室。由于传递窗一般设有气幕或紫外线,以及洁净室内的正压,可防止尘埃进入洁净室。亦可将灭菌柜(一般为隧道式)安装在传递窗内,一端开门于生产区,另一端开门于洁净室,物料从生产区装入灭菌柜,灭菌后经另一端(洁净室)取出。
3.内部结构要求 主要对地面和墙壁所用材料以及设计有一定的要求,材料应具备防湿、防霉,不易块裂、燃烧,耐磨性、导电性好,经济实用等性质,设计应满足不易染尘、便于清洗等。
五、洁净室的空气净化系统
(一)空气净化系统的设计要求
空气净化系统是保证洁净室洁净度的关键,该系统的优劣直接影响产品质量。空气中所含尘粒的粒径分布较广,为了有效地滤除各种不同粒径的尘埃,高效空气净化系统采用三级过滤装置:初效过滤→中效过滤→高效过滤(见图3-11)。中效空气净化系统采用二级过滤装置:初效过滤→中效过滤(图3-12)。系统中风机不仅具有送风作用,而且使系统处于正压状态。洁净室常采用侧面和顶部的送风方式,回风一般安装于墙下。

图3-11 高效空气净化系统

图3-12 中效空气净化系统
局部净化是彻底消除人为污染,降低生产成本的有效方法,特别适合于洁净度需100级要求的区域。一般采用洁净操作台、超净工作台、生物安全柜和无菌小室等,安装在10000级洁净区内。局部净化对输液和注射剂的灌封、滴眼剂和粉针的分装等局部工序具有较好的实用价值。
超净工作台(图3-8)是最常用的局部净化装置,其工作原理是使洁净空气(经高效过滤器后)在操作台形成低速层流气流,直接覆盖整个操作台面,以获得局部100级的洁净环境。送风方式有水平层流和垂直层流。其特点是设备费用少,可移动,对操作人员的要求相对较少。
(二)气流要求
由高效过滤器送出的洁净空气进入洁净室后,其流向的安排直接影响室内洁净度。气流形式有层流和乱流。
1.层流 系指空气流线呈同向平行状态,各流线间的尘埃不易相互扩散,亦称平行流。该气流即使遇到人、物等发尘体,进入气流中的尘埃也很少扩散到全室,而是随平行流迅速流出,保持室内洁净度,常用于100级洁净区。
层流分为水平层流和垂直层流(图3-13)。垂直层流以高效过滤器为送风口,布满顶棚,地板全部为回风口,使气流自上而下地流动;水平层流的送风口布满一侧墙面,对应墙面为回风口,气流以水平方向流动图,图3-14为水平层流洁净室空气示意图。

图3-13 层流气体示意图
1.风机;2.高效空气滤过器;3.回风夹层风道;4.回风口

图3-14 水平层流洁净室空气示意图
2.乱流 系指空气流线呈不规则状态,各流线间的尘埃易相互扩散,亦称紊流。乱流可获得1000~100000级的洁净空气。